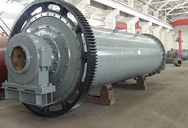
Coal for cement: Present and future trends
01 March 2016 Coal provides around 90% of the energy consumed by cement plants around the world, despite the environmental harm caused by its combustion. It takes 200
Charlar en Línea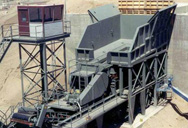
Coal and its application in the cement production process
2021.8.29 What role does coal play in cement production? Coal plays a very important role for manufacturing plants is undeniable. In many applications from gasification technology, liquefaction, production of
Charlar en Línea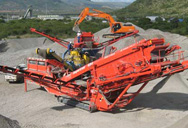
alternative energy sources in cement manufacturing
Cement manufacturing is an energy-intensive process with thermal and electric energy typically accounting for 40% of operational costs (European Commission, 2010). Fossil
Charlar en Línea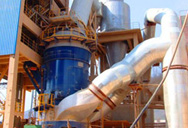
Deep Decarbonization of the Cement Sector: A Prospective
2021.12.11 In this study, a prospective environmental analysis has been conducted through life cycle thinking to explore the benefits of cement long-term decarbonization by
Charlar en Línea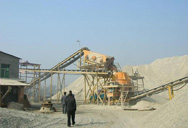
Coal utilisation in the cement and concrete industries
2013.1.1 1. As a fuel in the production of cement clinker, 2. Ash produced by burning coal in power stations is used as a component in cement rotary kiln feeds, 3.
Charlar en Línea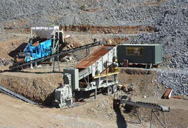
Recent development on the uses of alternative fuels in
2015.4.1 Cement manufacturing is one of the leading energy consuming and heavy pollutant processes which is accountable for CO 2, NO X, SO 2 emissions and some
Charlar en Línea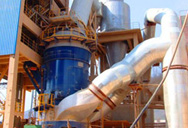
LCA and negative emission potential of retrofitted cement
2022.5.27 Main stages of the conventional cement production process (a) and retrofitted cement plants for oxyfuel combustion and CO 2 capture (b). Product systems
Charlar en Línea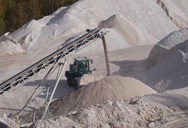
Investigation of environmental and exergetic performance
2012.10.1 Investigation of environmental and exergetic performance for coal-preparation units in cement production processes - ScienceDirect Energy Volume 46,
Charlar en Línea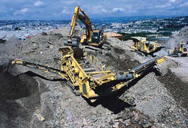
Deep decarbonisation of industry: The cement sector - europa
temperatures required in the cement manufacturing process, but has not yet been tested. As hydrogen’s combustion and the heat transfer (by radiation) in the kiln would differ
Charlar en Línea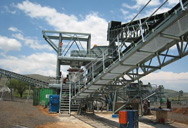
Environmental Impact Analysis of Portland Cement
2022.4.6 Cement plants in South Africa use fossil fuel (Coal) for their process and the kiln is the main energy-consuming stage in the entire cement production process. In South Africa, the energy consumption
Charlar en Línea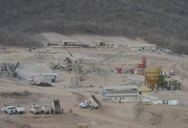
Carbon and air pollutant emissions from China’s cement industry
2012 and accounting for 6% of the total industrial coal use (China Cement Association, 2015). It is a major CO2 emitter due to high energy intensity and the dissociation of carbon-ate during the clinker production process. At the same time, the cement industry contributes substantially to the emissions of air pollutants, especially particles, ...
Charlar en Línea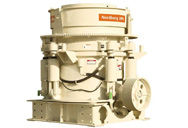
Parametric Studies of Cement Production Processes
2019.11.13 In cement production processes, there are several models for the purpose of studying the use of alternative fuels [4, 36, 39]: phase chemistry , oxidation process of coal tar pitch , cement raw
Charlar en Línea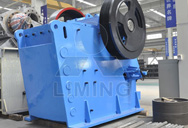
ACP - Carbon and air pollutant emissions from China's cement
2021.2.8 The cement industry is energy-intensive, representing 208 million t of coal consumption in 2012 and accounting for 6 % of the total industrial coal use (China Cement Association, 2015). It is a major CO 2 emitter due to high energy intensity and the dissociation of carbonate during the clinker production process.
Charlar en Línea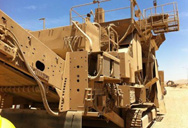
Integrated Pollution Prevention and Control (IPPC) Reference
At present, about 78% of Europe's cement production is from dry process kilns, a further 16% of production is accounted for by semi-dry and semi-wet process kilns, with the remainder of European production, about 6%, coming
Charlar en Línea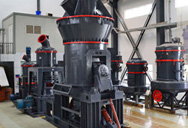
Options for switching UK cement production sites to near zero
Options for switching UK cement production sites to near zero CO 2 emission fuel: Technical and financial feasibility. ... Coal Fuel Specification for Coal Fired Baseline ..... 29 ii. Biomass Fuel Specification ... Cement manufacturing process [source: “Technology Roadmap: Low-
Charlar en Línea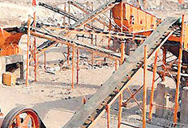
Energy and Economic Comparison of Different Fuels in Cement Production ...
2021.5.3 Energy cost contributes to about 40–50% of cement production cost in Nigeria depending on the production process and type of cement with 1 tonne of cement requiring 60–130 kg of fuel or its equivalent and about 105 kWh of electricity [ 3 ]. Fossil fuels like coal, pet coke, fuel oil, and gas are the primary fuels used in the cement kilns.
Charlar en Línea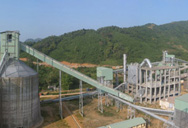
Alternative Clinker Technologies for Reducing Carbon Emissions in ...
2021.12.28 In fact, the production of one ton of clinker releases about 0.83 tons of CO 2 and the production of one ton of OPC releases about 0.54 ton of CO 2 making this industry responsible for 5% to 8% of total anthropogenic greenhouse gases The two main sources of CO 2 emissions resulting from cement production are: (i) the decarbonation
Charlar en Línea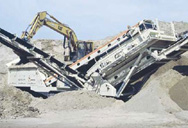
Cement Analysis and Production Information - Thermo Fisher
The cement production process begins with the extraction of limestone and clay from the quarry. The material is then blended, crushed and fed to the kiln. Post-kiln, the clinker is cooled and goes through a final grinding method before it is ready to ship. Portland cement, the most common type of cement, is formulated in a variety of strengths ...
Charlar en Línea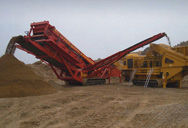
Improving the sustainability of cement production by using
2015.2.1 The cement industry sector is one of the largest carbon emitting industrial sectors, and due to the effect of global warming sustainable cement production is increasingly gaining on importance. Controlling the combustion of coal and the thermal degradation of limestone, the two main thermo-chemical processes that occur inside a
Charlar en Línea
BIOMASS ENERGY FOR CEMENT PRODUCTION: OPPORTUNITIES
The production process of cement clinker is energy-intensive and requires a large amount of fuel. Table 1 shows the increase in fuel consumption experienced by Mugher Cement plant over time. Table 1. Furnace Oil Consumption by Mugher Cement Plant, 1999-2000 (Taddele, 2008) Year Fuel Consumed (litres) Fuel (Birr)
Charlar en Línea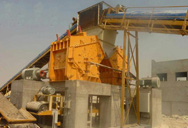
Cement - Wikipedia
The cement production process is responsible for near 8% ... Most cement kilns today use coal and petroleum coke as primary fuels, and to a lesser extent natural gas and fuel oil. Selected waste and by-products
Charlar en Línea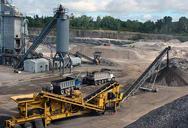
1,2,* , Oludolapo A. Olanrewaju , Kevin J. Duffy
2022.4.6 energy use [5,6]. Many countries (especially developing countries) use coal as a calcination fuel and emit large GHGs. Globally, the calcination process accounts for 50% of the total CO2 emissions from cement production, and others come from burning fuel in the kiln [7–9]. The amount of clinker (the primary ingredient) used in cement
Charlar en Línea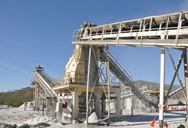
Analysis of material flow and consumption in cement production process ...
2016.1.20 The results show that approximately 2.48 t, 4.69 t, and 3.41 t of materials are required to produce a ton of the product in raw material preparation, clinker production, and cement grinding stages, and their waste rates are 63.31%, 74.12%, and 78.89%, respectively. The recycling rate of wastes during clinker production is remarkably higher
Charlar en Línea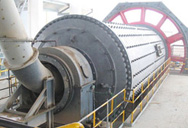
Life cycle assessment of a cement plant in Naypyitaw, Myanmar
2021.6.1 Approximately 60–65% of the primary calcination takes place in the pre-calciner utilizing almost 40% of the fuel energy. Kilns usually use coal and natural gas fuel mixes, heating the raw meal to about 1400–1500 °C. This stage is not only the most energy-intensive throughout the cement production process, but also the highest GHG
Charlar en Línea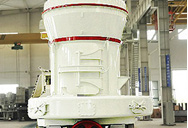
Cement - Extraction, Processing, Manufacturing Britannica
Extraction and processing. Raw materials employed in the manufacture of cement are extracted by quarrying in the case of hard rocks such as limestones, slates, and some shales, with the aid of blasting when necessary. Some deposits are mined by underground methods. Softer rocks such as chalk and clay can be dug directly by excavators.. The
Charlar en Línea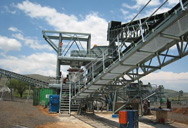
How is Cement Made? [2023] - Specifier Australia
There are many different types of cement factories – wet process, dry process and semi-dry process. The dry and semi-dry cement factories use rotary kiln technology. These cement manufacturers use Vertical shaft cement kilns which are the most common way of making cement all over the world. Average Cement Production
Charlar en Línea
Use of electrical energy in cement production [1,4]
The cement industry is an energy-intensive industry with energy typically accounting for 30–40% of production costs. Figure 1 presents the distribution of electricity demand in each stage of the ...
Charlar en Línea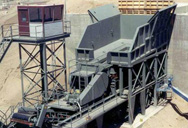
CO2 Capture, Use, and Storage in the Cement Industry: State of
2020.10.30 50% global cement production capacity. In 2019, GCCA launched Innovandi, the Global Cement and Concrete Research Network, which intends to research areas such as the impact of co-processing, the Figure 1. Scheme of a state-of-the art cement manufacturing process.
Charlar en Línea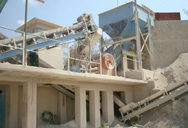
Fire Free Full-Text Modern Kiln Burner Technology in the ... - MDPI
The current manuscript presents a review on existing kiln burner technologies for the cement production process, in the context of the current climate of energy transition and environmental remediation. Environmental legislation has become ever stricter in response to global climate change, and cement plants need to adapt to this new reality in order to
Charlar en Línea