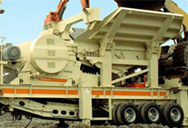
Improved iron recovery from low-grade iron ore by efficient
2022.8.1 Zhong et al. performed a pilot test of the coal-based direct reduction of a low-grade iron ore and obtained iron ore powder with the total iron recovery of 85.61% after the magnetic separation of the direct reduction products (Zhong et al., 2020).
Charlar en Línea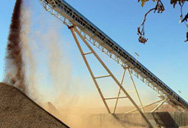
Dry separation of particulate iron ore using density
2013.3.1 We applied the dry density-segregation in a gas–solid fluidized bed to
Charlar en Línea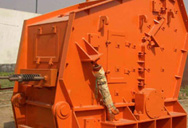
A new approach for recovering iron from iron ore tailings
2020.2.1 Moreover, the SMR technique and equipment have achieved
Charlar en Línea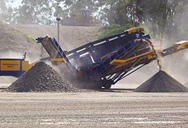
Dry separation of particulate iron ore using density-segregation in
2013.3.1 We applied the dry density-segregation in a gas–solid fluidized bed to
Charlar en Línea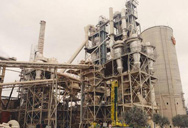
Agglomeration of Iron Ores SpringerLink
2023.6.11 Iron ore powder agglomeration is the basis for blast furnace
Charlar en Línea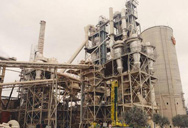
Minerals Free Full-Text Recovering Iron from Iron Ore
2019.4.15 Iron ore tailings (IOTs) are a form of solid waste produced during the beneficiation process of iron ore concentrate. In this paper, iron recovery from IOTs was studied at different points during a process
Charlar en Línea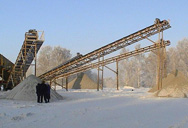
A new iron recovery and dephosphorization approach from high ...
2023.1.1 A new approach for simultaneous iron recovery and dephosphorization
Charlar en Línea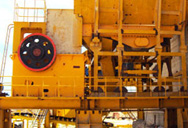
Physiochemical separation of iron ore - ScienceDirect
2022.1.1 Iron ore flotation. Froth flotation is an efficient method to remove
Charlar en Línea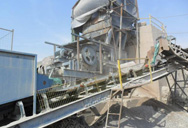
Preparation of Reduced Iron Powder from High-Phosphorus Iron
2023.7.3 Dephosphorization is essential for utilizing high-phosphorus iron ore
Charlar en Línea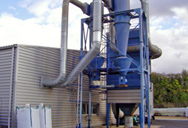
A new iron recovery and dephosphorization approach from high ...
2023.1.1 Deep dephosphorization of high‑phosphorus oolitic iron ore (HPOIO) is extremely difficult because of its refractory characteristics. A new approach for simultaneous iron recovery and dephosphorization from HPOIO by oxidation roasting – gas-based reduction (ORGR) and magnetic separation process was developed. The underlying
Charlar en Línea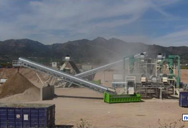
Minerals Free Full-Text Recovering Iron from Iron
2019.4.15 Iron ore tailings (IOTs) are a form of solid waste produced during the beneficiation process of iron ore concentrate. In this paper, iron recovery from IOTs was studied at different points during a
Charlar en Línea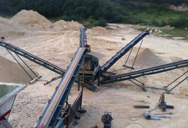
Magnetization roasting process of iron ores in the
Therefore, the ore was subjected to a high-temperature reduction roasting process between 800 • C and 1000 • C. Additionally, the magnetic separation process was also employed. The influence ...
Charlar en Línea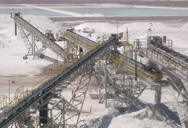
A novel direct reduction-flash smelting separation process of treating ...
2021.1.2 Deep dephosphorization of high‑phosphorus oolitic iron ore (HPOIO) is extremely difficult because of its refractory characteristics. A new approach for simultaneous iron recovery and dephosphorization from HPOIO by oxidation roasting–gas-based reduction (ORGR) and magnetic separation process was developed.The underlying
Charlar en Línea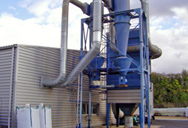
Production of magnetite nanoparticles from Ethiopian iron ore
2020.10.30 In this work, 60 g of iron ore powder and 90 ml of HCl were mixed in a beaker and stirred at different leaching temperature (60 °C, 80 °C, ... [30] MAO X H and LIU D J 2013 Solvent extraction separation of titanium(IV) and iron(III) from acid chloride solutions by trioctylphosphine oxide Asian J. Chem. 25 4756.
Charlar en Línea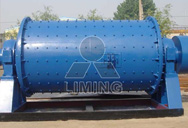
Ferrosilicon Powder - 911 Metallurgist
2018.4.15 Ferrosilicon powder (containing approx. 15% Si) for constitution of heavy media is used today in many separation plants treating iron and other ores. The production of the powder by grinding is expensive. A new process atomizes the still molten ferrosilicon by air or steam.
Charlar en Línea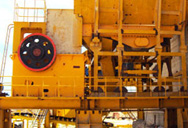
A new approach for recovering iron from iron ore tailings using ...
2020.2.1 Iron ore tailings, which are important secondary resources, have outstanding latent application value in iron recovery. In this study, a pilot-scale experiment on the iron recovery from iron ore tailings was investigated using innovative technology of pre-concentration and suspension magnetization roasting (SMR), followed by magnetic
Charlar en Línea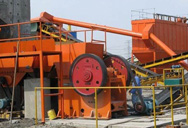
A review on the enrichment of iron values of low-grade Iron ore ...
2020.5.1 The beneficiation of low-grade iron ores to meet the growing demand for iron and steel is an important research topic. However, certain ores do not qualify to be treated in physical separation processes, and hence, alternative strategies are being looked into for upgrading their iron content.
Charlar en Línea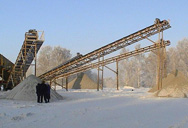
Innovative methodology for comprehensive utilization of iron ore ...
2010.2.15 Iron ore tailings have become one kind of the most hazardous solid waste. In order to recycle iron in the tailings, we present a technique using magnetizing roasting process followed by magnetic separation. After analysis of chemical composition and crystalline phase, according to experimental mechanism, the effects of different
Charlar en Línea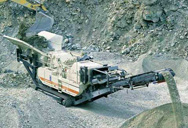
Preparing Ferro-Nickel Alloy from Low-Grade Laterite Nickel Ore
2017.8.16 Nickel, a valued metal, mainly exists as nickel oxide in laterite nickel ore. Furthermore, a large part of the laterite nickel ore is low-grade saprolitic ore. In this paper, a research on preparing ferro-nickel alloy from low-grade saprolitic laterite nickel ore using metallized reduction-magnetic separation was studied. In the research, the carbothermic
Charlar en Línea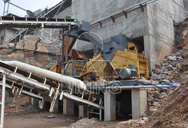
Microwave-Intensified Separation of Boron and Iron from Ludwigite Ore ...
2023.10.6 However, the separation of boron and iron by traditional pyrometallurgical processes faces many challenges. 8,9 For instance, the boron-rich slags prepared by both the blast furnace smelting method based on sintering of ludwigite ore and the electric furnace smelting method based on pre-reduction of the ore have low activity, which must
Charlar en Línea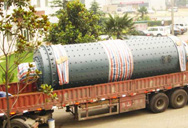
Magnetic separation studies for a low grade siliceous iron ore sample ...
2013.1.1 Conclusions. The investigations carried out on the low grade iron ore sample reveal the following conclusions. (1) The sample on average contains 43.8% Fe, 16.8% SiO 2 and 5.61% Al 2 O 3. (2) The mineralogical studies indicate that the major iron minerals are magnetite, hematite and goethite. And the gangue minerals are silicates
Charlar en Línea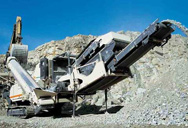
High-efficiency extraction of iron from early iron tailings via the ...
2021.2.1 The high-efficiency extraction of iron from early iron tailings via the innovative suspension roasting-magnetic separation (SRMS) technology would be an important method to consolidate the available iron ore resources. In this study, the roasting effect and product characterizations of SRMS were investigated by the SRMS tests, X
Charlar en Línea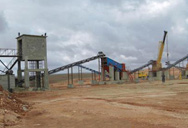
An efficient and green method to separate iron and manganese
2022.4.1 Traditional processes can't treat low-grade iron ore and are unable to transform the phase of iron minerals, thus they are very inefficient. To solve these problems, a novel method was proposed in this work for enhancing iron extraction and dephosphorization from high phosphorus limonite by suspension magnetization roasting
Charlar en Línea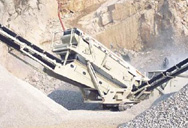
Microwave-assisted reduction roasting—magnetic separation studies
2020.11.9 The microwave-assisted reduction behaviours of two low-grade iron ores having a similar Fe content of 49wt% but distinctly different mineralogical and liberation characteristics were studied. Their performances in terms of the iron grade and recovery as obtained from statistically designed microwave (MW) roasting followed by low-intensity
Charlar en Línea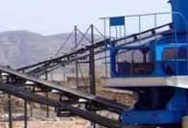
Novel Technology for Comprehensive Utilization of Low-Grade Iron Ore
2022.4.18 In this study, a novel technology for the comprehensive utilization of low-grade iron ore is presented. For the iron ore with a Fe content of 24.91%, a pilot-scale study of pre-concentration, suspension magnetization roasting, grinding, and low-intensity magnetic separation was conducted, and an iron concentrate with a grade of 62.21%
Charlar en Línea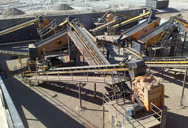
Extraction and separation of copper and iron from copper
2022.9.25 In 2021, China imported 23.404 million tons of copper ore and copper concentrate, and 1.12 billion tons of iron ore. The external dependence of both copper and iron exceeded 80%, which posed a great threat to the healthy and sustainable development of China's non-ferrous industry, iron and steel industry and even the national economy
Charlar en Línea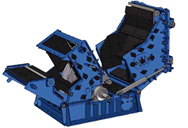
Materials Free Full-Text High-Efficiency Iron Extraction from Low ...
2022.9.8 Upgrading and utilizing low-grade iron ore is of great practical importance to improve the strategic security of the iron ore resource supply. In this study, ... A review on the enrichment of iron values of low-grade Iron ore resources using reduction roasting-magnetic separation. Powder Technol. 2020, 367, 796–808. [Google Scholar]
Charlar en Línea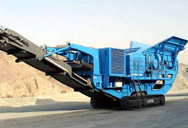
Comprehensive Utilization of Iron and Phosphorus from High
2017.11.6 Recent studies have found that direct reduction followed by magnetic separation is one of the most feasible methods to recover iron from refractory iron ores.1,2 It was reported that by using this process, more than 90% of iron could be recovered as direct reduced iron (DRI) powder.3,4, – 5 Nevertheless, the phosphorus content in DRI
Charlar en Línea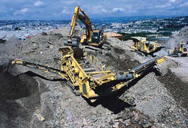
A novel direct reduction-flash smelting separation process of
2021.1.2 The HPIO used in this study is produced in Hubei, China, and its main components are listed in Table 1.It can be seen from the scanning electron microscope that the iron ore particles have a clear oolitic structure, as shown in Fig. 1.The layered structure is mainly composed of hematite, apatite or chlorite, and the silica‑aluminum impurities or
Charlar en Línea