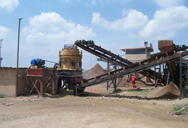
Ball Mill Design/Power Calculation - 911 Metallurgist
2015.6.19 If P is less than 80% passing 70 microns, power consumption will be Ball Mill Power Calculation Example #1 A wet
Charlar en Línea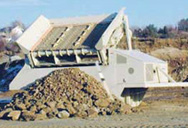
Charge behaviour and power consumption in ball mills:
2001.8.1 Typical power consumption for a 5-m diameter by 7-m-long ball mill is between 2.5 and 3.5 MW. The actual proportion of this energy usefully used in size
Charlar en Línea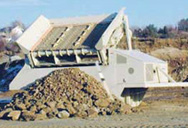
Charge behaviour and power consumption in ball mills:
2001.8.1 Typical power consumption for a 5-m diameter by 7-m-long ball mill is between 2.5 and 3.5 MW. The actual proportion of this energy usefully used in size
Charlar en Línea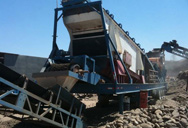
(PDF) Energy Efficient Ball Mill Circuit – Equipment Sizing ...
2013.7.15 The ball mill in closed circuit with hydrocyclones is an industry standard, and well known methodologies exist for equipment
Charlar en Línea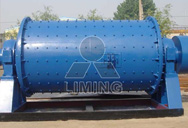
Modeling of energy consumption factors for an industrial ... - Nature
2022.5.9 XGBoost has accurately estimated the vertical roller mill's output temperature and motor power based on the plant monitoring variables (R-square over
Charlar en Línea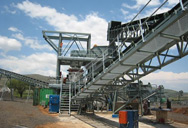
(PDF) Performance optimization of an industrial ball mill
2017.1.1 In this investigation, we optimize the grinding circuit of a typical chromite beneficiation plant in India. The run-of-mine ore is reduced to a particle size of less than 1 mm in the comminution ...
Charlar en Línea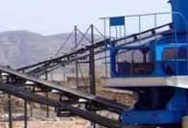
Effects of Ball Size Distribution and Mill Speed and Their
2020.7.2 When the mills charge comprising 60% of small balls and 40% of big balls, mill speed has the greatest influence on power consumption. When the mill charge is
Charlar en Línea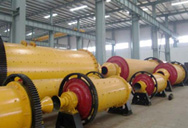
Calculation method and its application for energy
Measurement results of two ball mills in a real ceramic manufacturing plant showed that the proposed calculation models could achieve an accuracy of more than 96% for predicting
Charlar en Línea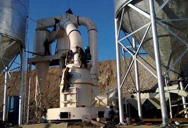
Ball charge loading - impact on specific power consumption and
2006.5.30 The research concludes that lowering the ball mill filling percentage negatively affects mill sizing and increases capital and installation costs of milling
Charlar en Línea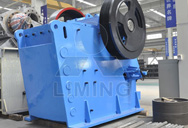
Charge behaviour and power consumption in ball mills: Sensitivity
2001.8.1 The developed code was used to examine the influence of three lifter profiles and mill speeds on the granular dynamics and power consumption of a
Charlar en Línea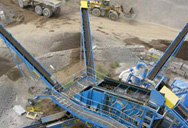
Effects of Mill Speed and Air Classifier Speed on Performance of
Results, typically of power consumption have been over served as skewed in a lab scale ball mill, when compared to the industrial scale ball mill [5]. Likewise, the ambient conditions, climate, raw material and human factor could also impact the performance of ball mill [6]. Therefore, some type of calibration is required in the as obtained
Charlar en Línea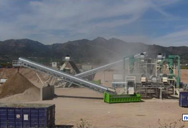
Power Calculation of Ball-Tube Mill Drives in the Construction ...
2023.5.12 The main equipment for grinding construction materials are ball-tube mills, which are actively used in industry and are constantly being improved. The main issue of improvement is to reduce the power consumption of a ball-tube mill with cross-longitudinal movement of the load. A comparative analysis and the possibility of using the
Charlar en Línea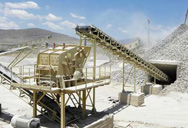
Improving product quality in pharmaceutical ball milling
2021.8.2 Ball milling is used in the pharmaceutical industry to reduce the size of particulate material such as pharmaceutical granules. Dr Alexander Krok and Dr Sandra Lenihan from Munster Technological University, Ireland, have developed a computational approach to achieve optimal, energy-efficient size reduction in ball milling resulting in the
Charlar en Línea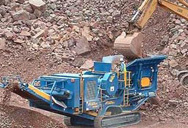
Energy Efficiency Analysis of Copper Ore Ball Mill Drive
2021.2.26 Analysis of Variant Ball Mill Drive Systems. The basic element of a ball mill is the drum, in which the milling process takes place ( Figure 1 ). The length of the drum in the analyzed mill (without the lining) is 3.6 m, and the internal diameter is 3.4 m. The mass of the drum without the grinding media is 84 Mg.
Charlar en Línea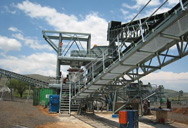
How to reduce the energy consumption of ball mill - LinkedIn
2021.6.2 In order to reduce the power consumption of the ball mill, the feed particle size of grinding can be reduced. Therefore, the product particle size of crushing is required to be small, that is to ...
Charlar en Línea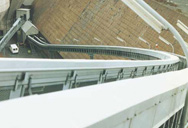
(PDF) Performance optimization of an industrial ball mill for
2017.1.1 The power consumption of the ball mill was monitored for. ... It is important to avoid agglomeration and reduce the power consumption per ton ore produced. 22 However, ...
Charlar en Línea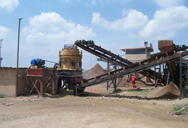
Ball Mill - an overview ScienceDirect Topics
A feature of ball mills is their high specific energy consumption. A mill filled with balls, working idle, consumes approximately as much energy as at full-scale capacity, that is, during the grinding of material. Therefore, it is most disadvantageous to use a ball mill at less than full capacity.
Charlar en Línea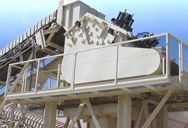
Energy conservation and consumption reduction in
2023.11.1 The ball mill on site, has problems such as uneven product particle size, low grinding efficiency, insufficient dissociation degree of useful mineral monomers, and high grinding energy consumption[[20], [21], [22], [33], [34]].The existing technological process of the first beneficiation workshop of Gongchangling Concentrator is as follows: two
Charlar en Línea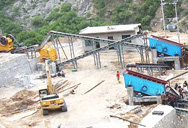
Optimization of Cement Grinding Operation in Ball Mills PEC ...
Optimization of the Cement Ball Mill Operation. Optimization addresses the grinding process, maintenance and product quality. The objective is to achieve a more efficient operation and increase the production rate as well as improve the run factor. Consistent quality and maximum output with lower specific power consumption results in lower ...
Charlar en Línea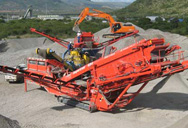
(PDF) Energy conservation and consumption reduction in
2023.9.1 This paper demonstrates the feasibility of using a ceramic medium stirring mill to reduce the energy consumption . ... Where P, P 0 and I 0 refer separately to the ball mill's working power (kW), ...
Charlar en Línea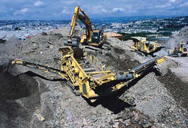
(PDF) A Comparative Study of Energy Efficiency in Tumbling Mills
2021.4.29 Standard Bond tests showed a reduction in the Bond ball mill work index (wi) of the mineral sample used in this study when using Relo grinding media. The modified Bond test procedure is based on ...
Charlar en Línea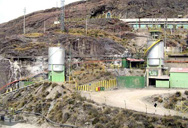
(PDF) Energy Efficient Ball Mill Circuit – Equipment
2013.7.15 A power-based method is first utilised to determ ine the required ball mill power consumption to . achieve the required product P80. ... used to reduce the selected ball mill size and power.
Charlar en Línea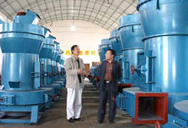
Reduce Energy Consumption: Cement Production - Control
2011.8.25 Drives also are used to power roller mills for grinding different blaine of slag for cement, and for starting and running multiple roller mills, ball mills, and overland conveyors. A China-based cement plant used VFDs to significantly reduce its energy consumption in its dry-process kilns, responsible for production of 1.4 million tons of
Charlar en Línea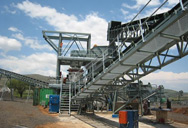
Ball Mill Design/Power Calculation - DESIGN AND ANALYSIS OF BALL MILL
2015.6.19 If PIANO is less than 80% go 70 microns, power consumption will be; Ball Roller Power Calculation Model #1. A wet grinding ball mill in closed circuit is to be detective 100 TPH of a substance with a work index of 15 and a size distributor of 80% passing ¼ inch (6350 microns).
Charlar en Línea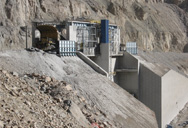
Charge behaviour and power consumption in ball mills:
2001.8.1 Discrete element method (DEM) modelling has been used to systematically study the effects of changes in mill operating parameters and particle properties on the charge shape and power draw of a 5-m ball mill. Specifically, changes in charge fill level, lifter shape (either by design or wear) and lifter pattern are analysed. The effects of
Charlar en Línea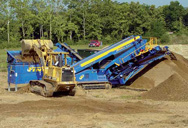
A Comparative Study of Energy Efficiency in Tumbling Mills with
Tumbling mills are notorious for their low energy efficiency because they only use up to 10% of installed power for grinding action. A feature of ball mills is their high specific energy consumption; a mill filled with balls, working idle, consumes approximately as much energy as at full-scale capacity, i.e., during the grinding of material.
Charlar en Línea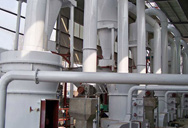
Energy Use of Fine Grinding in Mineral Processing
2013.12.18 Fine grinding, to P80 sizes as low as 7 μm, is becoming increasingly important as mines treat ores with smaller liberation sizes. This grinding is typically done using stirred mills such as the Isamill or Stirred Media Detritor. While fine grinding consumes less energy than primary grinding, it can still account for a substantial part of a
Charlar en Línea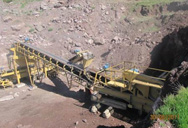
A Technical and Economic Comparison of Ball Mill Limestone
2021.10.13 A pilot-scale Loesche VRM was used to determine the power required to grind 100 t/h of the same limestone as used at Kusile (work index of 12 kWh/t) with a top size of 19 mm to a 85% and 95% passing 45 µm product. A significant power saving of 39.2% was observed for the dry VRM compared to the wet ball mill (37.7% for the circuit).
Charlar en Línea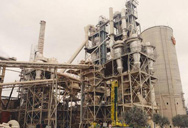
Comparative comminution efficiencies of rotary, stirred and
2021.7.15 The vibratory ball mill (VBM, Sweco, ... Milling energy consumption. For all experiments, the power of the milling devices was measured using a PX 120 wattmeter (METRIX, ... as it demanded 37% of the bark energy content and as high as 220% of the straw energy content to reduce these materials into 20 μm powders.
Charlar en Línea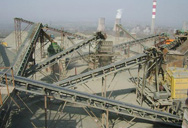
Estimation of the Specific Energy Requirement for Size
2016.11.8 Every year billions of tons of metallic ores, minerals, cement and various other solids are ground in the ball mills. It is well known that grinding of solids is an energy intensive operation. Typically, the specific energy necessary to reduce the feed material to the desired product size varies in the range of 5–50 kWh/t.
Charlar en Línea