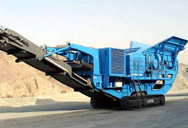
Original Research PaperEnergy and cement quality
2018.7.1 The calculations implied that the production rate increased by 4.45% that corresponded to energy saving of 4.26%. As the plant decided to change the flow
Charlar en Línea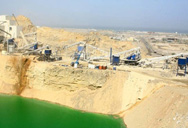
PROCESS OPTIMISATION FOR LOESCHE GRINDING PLANTS
Coal Cement raw material Clinker / granulated slag Industrial minerals, and Ores The core elements of these plants are the Loesche vertical mills for dry-grinding the above
Charlar en Línea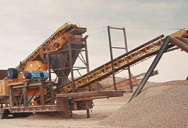
Coal Grinding - Cement Plant Optimization
Coal Mill Operational parameters: Mill Load (Kw or Amps). Mill sound/filling % (in ball mills). Mill Inlet Temperature (0 C). Mill Outlet Temperature (0 C). Gas flow through mill (m 3
Charlar en Línea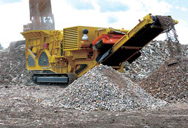
Typical cement manufacturing process flow diagram
This paper mainly reveals the industrial process like cement industry, coal fire power plants, aluminium plants, and fired power plants. We finally discussed the challenges of the chemical ...
Charlar en Línea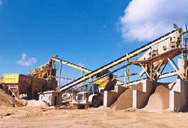
Schematic flow-sheet of a multi-stage grinding plant for the
Download scientific diagram Schematic flow-sheet of a multi-stage grinding plant for the production of Portland-cements including 3 different grinding steps (GS). from
Charlar en Línea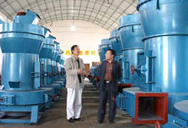
11.6 Portland Cement Manufacturing - U.S. Environmental
Q. Raw mill air seperator -26 R. Finish grinding mill feed belt -27 S. Finish grinding mill weight hopper -28 T. Finish grinding mill air seperator -29 U. Preheater kiln 3-05-006-22 V. Preheater/Precalciner kiln 3-05-006-23 The second step in portland cement manufacture is preparing the raw mix, or kiln feed, for the
Charlar en Línea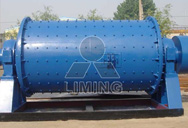
Coal Grinding - Cement Plant Optimization
Coal Grinding. To achieve good combustion and satisfactory flame formation, coal needs to be dried and ground to a proper degree of dryness and fineness. Drying of moisture in coal is achieved normally by ducting part of the kiln exhaust gas through the mill with inlet temperatures of up to 300°C. Inert kiln exhaust gases with oxygen content ...
Charlar en Línea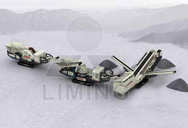
Simulation aided flow sheet optimization of a cement grinding
2016.11.1 The simplified flow sheet of the cement grinding circuit together with the sampling points is shown in Fig. 2. ... A simulation model for an air-swept ball mill grinding coal. Powder Technol. (1984) H. Benzer et al. Modelling cement grinding circuits. Miner. ... As the plant decided to change the flow sheet, ...
Charlar en Línea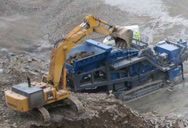
Energy and cement quality optimization of a cement grinding circuit ...
2018.7.1 As the plant decided to change the flow sheet, another sampling campaign was arranged to validate the outputs of the simulation studies. In that case, the real data showed that the increase in production rate was 3.68% and 28-Days strength of the cement improved by 2.9%.
Charlar en Línea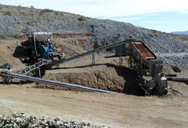
Cement plant coal mill grinding flow sheet
5 Jul 2023; A cement plant coal mill grinding flow sheet represents the process of processing coal in the grinding system of a cement plant. The flow sheet illustrates the steps that coal and other raw materials undergo during the production of cement. It explains the order of various stages of the grinding and drying process, which helps achieve the
Charlar en Línea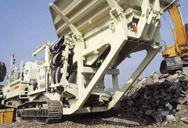
Coal Mill in Cement Plant
It is a mechanical device used to grind raw coal into pulverized coal powders. The most used coal mills in cement plants are air-swept ball mills and vertical roller mills. At present, most cement plants use coal as the main fuel in the clinker production process. The standard coal consumed by the new dry process for producing 1 ton of cement ...
Charlar en Línea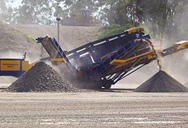
ATOX® Coal Mill - FLSmidth
Our ATOX® Coal Mill has large rollers with great grinding capability of virtually all types of raw coal. The rollers work harmoniously with a highly-efficient separator and feed sluice to consistently and reliably deliver coal meal to your desired fineness and moisture level. ATOX® Coal Mill. what we offer key benefits product features downloads.
Charlar en Línea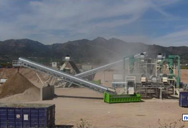
OPTIMIZING THE CONTROL SYSTEM OF CEMENT MILLING:
Mill Feed Sep. Return Final Product System Fan Figure 1: Closed circuit grinding system. milling system is a delicate task due to the multivari-able character of the process, the elevated degree of load disturbances, the different cement types ground in the same mill, as well as the incomplete or missing information about some key process charac-
Charlar en Línea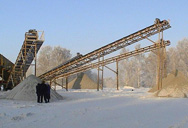
The Green Cement plant FLSmidth
OK™ raw mill – reliable, efficient raw material grinding Boosting energy efficiency and with a high run factor, the OK raw mill is a Green Cement flagship. UP TO 10% less power
Charlar en Línea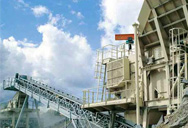
Jaypee Group Businesses Cement-Manufacturing Process
Limestone is extracted transversely from the stockpiles by the reclaimers and conveyed to the Raw Mill hoppers for grinding of raw meal. Crushing Stacking Reclaiming of Coal. The process of making cement clinker requires heat. Coal is used as the fuel for providing heat. Raw Coal received from the collieries is stored in a coal yard.
Charlar en Línea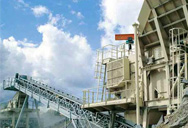
Premium solutions for the cement industry - FLSmidth
Are you looking to invest in a new plant, increase the capacity of an existing site, or investigating productivity improvements? As a full flowsheet provider with more than 140 years of experience in the cement industry, we are ready to assist you through the entire life-cycle of your plant.
Charlar en Línea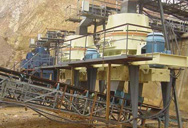
Scantogo HeidelbergCement Togo
Scantogo is a subsidiary of Scancem International, member of HeidelbergCement group. Type: Clinker Production plant Production Capacity: 1.5 million tons per year Start of production: November 2014
Charlar en Línea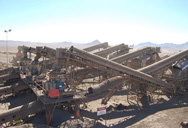
(PDF) Analysis of material flow and consumption in
2015.8.1 The results show that approximately 2.48t, 4.69t, and 3.41t of materials are required to produce a ton of the product in raw material preparation, clinker production, and cement grinding stages ...
Charlar en Línea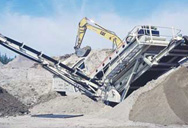
Raw Material Drying-Grinding - Cement Plant Optimization
Ball mills for cement raw material and coal equipped with a drying compartment adequately air swept with hot gas (2.5-3.5M/sec above the ball charge), can handle moisture about 8%. Fully air- swept mills (5-6M/sec) can dry up to 12-14% moisture. Grinding Operation Objectives and KPIs: Highly energy intensive unit operation of size reduction in ...
Charlar en Línea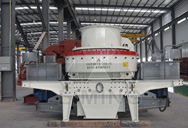
(PDF) Grinding Media in Ball Mills-A Review - ResearchGate
2023.4.23 flow inside the mill, showed that the collision energy of grinding media increased with mill speed from 22 to 45 rpm giving more undersized pr oduct of 15.2mm, 11.2mm and 8.6mm and sudde nly ...
Charlar en Línea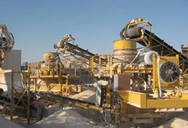
Cement Grinding Plant Overview Cement Grinding Unit AGICO Cement
2019.10.11 AGICO Cement is a cement grinding plant manufacturer, we'd like to helps you learn more about cement grinding plant and cement grinding machines. Skip to content +86 13683722138
Charlar en Línea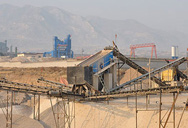
Typical cement manufacturing process flow diagram [4].
Process Flow diagram [12] (Model Development for CO2 Capture in the Cement Industry)5.2 Coal-Fired Power Plant. ... Post-Combustion Carbon Capture-Chemical Absorption Process Article
Charlar en Línea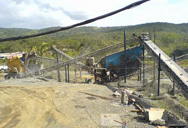
Cement Manufacturing Process Flowsheet (Flow Chart)
This is the ReadMe file of a SuperPro Designer example that simulates a cement manufacturing plant where cement clinker is produced by mixing clay and limestone. First, clay and limestone are ...
Charlar en Línea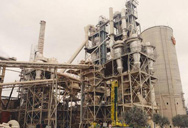
Coal Dust Explosions in the Cement Industry - Texas AM
coal grinding, drying, blending.transporting, and storing. Case histories investigated by the Mine Safety and Health Administration (MSHA) will be discussed, and recommendations will be made for future fire and explosion prevention. KEY WORDS: coal dust, fires and explosions, cement plants, coal fired systems, safety
Charlar en Línea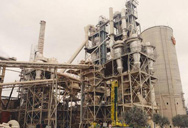
Advanced process control for the cement industry - FLSmidth
specifically for cement applications. With more than 40 years of plant automation experience, FLSmidth has installed over 700 control systems and 450 laboratory systems – and understands the needs of today’s cement plants. FLSmidth is a world leader in building and maintaining cement plants, and that first-hand experience plays an
Charlar en Línea