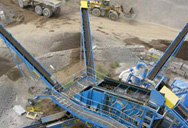
Comparison of energy efficiency between ball mills and
2009.6.1 Comparison of a laboratory vertical shaft stirred mill with a ball mill, both operated in a virtually closed circuit with a classifier, indicated that on average 30% energy saving can be expected by using the stirred mill to replace ball mill for coarse grinding.
Charlar en Línea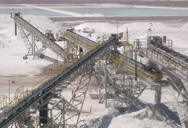
what is the difference between tube grinder and ball mill
2023.8.25 Key Differences: Geometry: The primary difference lies in the geometry of the grinding chambers. Tube mills have a longer cylindrical structure with a smaller
Charlar en Línea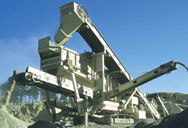
Ball mill - Wikipedia
A ball mill is a type of grinder used to grind or blend materials for use in mineral dressing processes, paints, pyrotechnics, ceramics, and selective laser sintering. It works on the principle of impact and attrition: size reduction is done by impact as the balls drop from near the top of the shell. A ball mill consists of a hollow cylindrical shell rotating about its axis. The axi
Charlar en Línea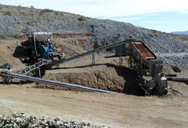
Ball Mill SpringerLink
2023.4.30 Ball mill is a type of grinding equipment that uses the rotary cylinder to bring the grinding medium and materials to a certain height and make them squeeze,
Charlar en Línea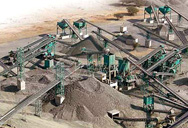
Ball Mill - an overview ScienceDirect Topics
Ball mills are commonly used for crushing and grinding the materials into an extremely fine form. The ball mill contains a hollow cylindrical shell that rotates about its axis. This
Charlar en Línea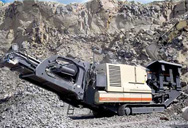
Comparison of energy efficiency between ball mills and stirred
2009.6.1 Ball mills are the most common and versatile type of tumbling mill. They are remarkable in that they can operate over a very wide range of conditions and
Charlar en Línea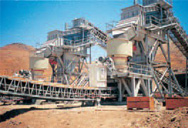
Mathematical validation and comparison of ball tube and bowl
2023.6.7 The ball tube mill requires less mass flow rate of primary air and raw coal per MW of power produced than the bowl mill. It contains larger mass of raw and
Charlar en Línea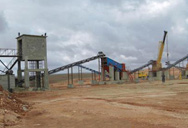
Mathematical validation and comparison DOI 10.1007/s12206
on-site data for the two mills and show good agreement. The ball tube mill requires less mass flow rate of primary air and raw coal per MW of power produced than the bowl
Charlar en Línea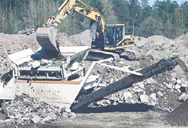
Tumbling Mill Mechanics SpringerLink
A tumbling mill is a collective name for the generally known ball mills, rod mills, tube mills, pebble mills and autogeneous mills. For all these kinds of mills the mechanics can be
Charlar en Línea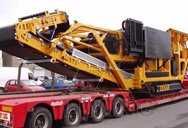
What’s the Difference Between SAG Mill and Ball Mill
2019.11.26 The biggest characteristic of the sag mill is that the crushing ratio is large. The particle size of the materials to be ground is 300 ~ 400mm, sometimes even larger, and the minimum particle size of the
Charlar en Línea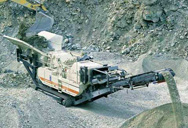
Hammer mill and Ball mill PPT - SlideShare
2021.1.11 Size separation RAHUL PAL. 23.9K views • 12 slides. Hammer mill and Ball mill - Download as a PDF or view online for free.
Charlar en Línea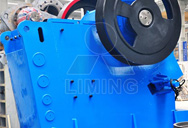
Difference Between Cement Vertical Mill and Ball Mill
Compared with the ball mill, the vertical mill can save 30% -40% of energy consumption, and has low vibration, which is a low energy consumption. Energy Saving and Noise Reduction When the vertical mill is in operation, the grinding roller does not directly contact the grinding disc, and the vibration is small, the noise is low, and the sound is soft.
Charlar en Línea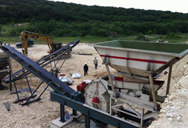
2 Process of Manufacture of Cement - Civil Giant
Clinkers are ground in ball mills and tube mills after controlled cooling. The cooling rate of clinkers affects the strength-gaining properties of cement. About 3-5 % gypsum is added during grinding to the cooled clinkers to prevent flash set. Closed-circuit grinding is done in tube mills. A cyclonic separator ensures proper particle size ...
Charlar en Línea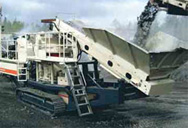
Ball Mill - an overview ScienceDirect Topics
8.3.2.2 Ball mills. The ball mill is a tumbling mill that uses steel balls as the grinding media. The length of the cylindrical shell is usually 1–1.5 times the shell diameter (Figure 8.11 ). The feed can be dry, with less than 3% moisture to minimize ball coating, or slurry containing 20–40% water by weight.
Charlar en Línea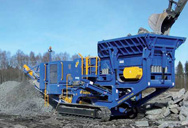
Operation of Tube Mills - Archive
This paper serves as general guide line for better mill operation and the procedure of practical mill assessment. In a cement plant, the largest portion of electrical energy costs is related to cement grinding. Any improvement in grinding efficiency results in considerable savings. Subsequent guide.
Charlar en Línea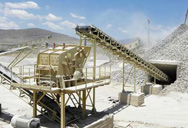
Tube Mills - 911 Metallurgist
2016.10.30 According to Gruessner, at the Hannan’s Star Mill, Kalgoorlie, the ore from two No. 5 dry ball mills was treated wet in a tube mill 16 feet 5 inches long and 3 feet 11 inches in diameter. The ball mills crushed 78 tons per day and, after classification, the coarser part of this, amounting to 38 tons, was ground to about 250 mesh in the tube mill.
Charlar en Línea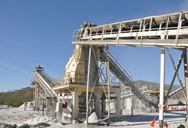
Mathematical validation and comparison DOI 10.1007/s12206
Ball tube mill Bowl mill Coal mill model Model coefficients Pulverized coal Raw coal Correspondence to: Chanpreet Singh [email protected] Citation: Singh, C., Singh, P. (2023). Mathematical validation and comparison of ball tube and bowl mill operations at steady state. Journal of Mechanical Science and
Charlar en Línea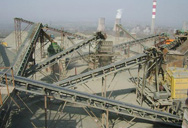
Study of Hammer mill and Ball mill - Centurion University
tumbler functions on the same principle. High quality ball mills are potentially expensive and can grind mixture particles to as small as 0.0001 mm, enormously increasing surface area and reaction rates. Ball mill: Ball mill is a type of crusher, is a cylindrical device used to grind or mix materials like ores, chemicals, ceramics and paints.
Charlar en Línea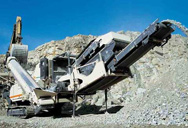
Ball tube mill PPT - SlideShare
2017.12.12 20.8K views • 43 slides. Ball tube mill - Download as a PDF or view online for free.
Charlar en Línea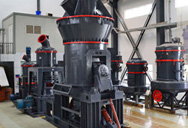
Ball Mill - Pharmacy Gyan Principle Construction
2021.11.16 Ball Mill. The ball mill’s basic concept dates back to prehistoric times when it was used to grind flint for pottery. A pharmaceutical ball mill is a type of grinder that is used to grind and combine materials
Charlar en Línea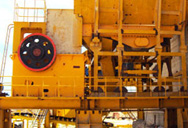
Cement grinding Vertical roller mills VS ball mills
For a ball mill grinding OPC to a fineness of 3200 to 3600 cm2/g (Blaine) the cost of wear parts (ball, liners and mill internals) is typically 0.15-0.20 EUR per ton of cement. For an OK mill grinding a similar product, the
Charlar en Línea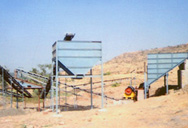
Ball Mill - an overview ScienceDirect Topics
Generally, filling the mill by balls must not exceed 30%–35% of its volume. The productivity of ball mills depends on the drum diameter and the relation of ∫ drum diameter and length. The optimum ratio between length L and diameter D,
Charlar en Línea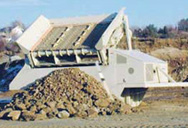
Ball mill - Wikipedia
A ball mill, a type of grinder, is a cylindrical device used in grinding (or mixing) materials like ores, chemicals, ceramic raw materials and paints. Ball mills rotate around a horizontal axis, partially filled with the material to be ground plus the grinding medium. Different materials are used as media, including ceramic balls, flint pebbles ...
Charlar en Línea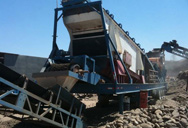
Ball Mill (Ball Mills Explained) - saVRee - saVRee
If a ball mill uses water during grinding, it is a ‘wet’ mill. A typical ball mill will have a drum length that is 1 or 1.5 times the drum diameter. Ball mills with a drum length to diameter ratio greater than 1.5 are referred to as tube mills. Ball
Charlar en Línea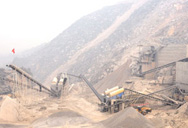
What is the difference between vertical mill and ball mill?
2022.1.12 Ultrafine vertical mills and ball mills are common large-scale industrial grinding equipment and are widely used. However, many people still do not know how to choose the most suitable equipment when purchasing equipment. Let’s take a look at the difference between ultrafine vertical mill and ball mill.
Charlar en Línea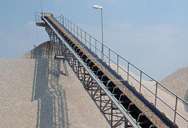
(PDF) System dynamics model of output of ball mill
2021.2.15 The ball tube mill requires less mass flow rate of primary air and raw coal per MW of power produced than the bowl mill. It contains larger mass of raw and pulverized coal but less grinding heat ...
Charlar en Línea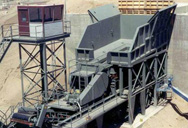
Comparison of energy efficiency between ball mills and stirred mills
2009.6.1 A comparative analysis of the ball mill and stirred mill performance and energy consumption at different grinding time intervals was also performed. It was found that the ball mill consumed 54.67 kWh/t energy to reduce the F 80 feed size of 722.2 µ m to P 80 product size of 275.4 µ m while stirred mill consumed 32.45 kWh/t of energy to
Charlar en Línea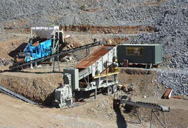
Construction and Working of Ball Mill - Solution Parmacy
2021.5.11 Construction of Ball Mill. The ball mill consists of a hollow metal cylinder mounted on a shaft and rotating about its horizontal axis. The cylinder can be made of metal, porcelain, or rubber. Inside the cylinder balls or pebbles are placed. The balls occupy between 30 and 50% of the volume of the cylinder. The diameter of the balls depends on ...
Charlar en Línea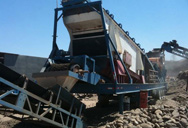
Pulveriser in Thermal Power Plant Bowl Mill Ball Mill
Operation of Ball Mill Pulveriser. The Ball mill pulveriser is basically horizontal cylindrical tube rotating at low speed on its axis, whose length is slightly more to its diameter. The inside of the Cylinder shell is fitted with heavy cast liners and is filled with cast or forged balls for grinding, to approximately 1/3 of the diameter.
Charlar en Línea