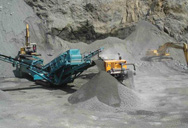
Investigation on measuring the fill level of an industrial
2009.11.1 Ball mill Fill level Vibration signal Coal 1. Introduction It is well established that the ball mill pulverizing system has exceptional adaptability for
Charlar en Línea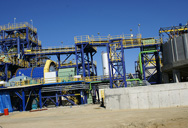
Proposed method to monitor the fill level of a ball mill
The fill level inside a ball mill is a crucial parameter which needs to be monitored regularly for optimal operation of the ball mill. In this paper, a vibration monitoring
Charlar en Línea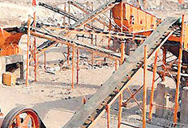
Investigation on measuring the fill level of an industrial ball mill ...
2009.11.1 As the ball mill pulverizing system is non-linear, has long time delays and time-varying, the fill level of the coal powder cannot be measured accurately, which
Charlar en Línea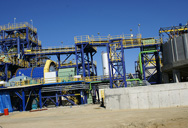
Monitoring the fill level of a ball mill using vibration sensing and ...
The fill level inside a ball mill is a crucial parameter which needs to be monitored regularly for optimal operation of the ball mill. In this paper, a vibration monitoring-based method
Charlar en Línea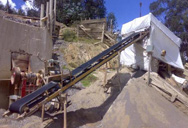
An improved method for grinding mill filling
2021.1.1 The new method offers engineers and researchers a safer and faster method for quantifying the filling level in industrial SAG and ball mills, and allows the
Charlar en Línea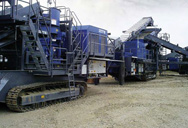
An improved method for grinding mill filling measurement and
2020.11.10 The new method offers engineers and researchers a safer and faster method for quantifying the filling level in industrial SAG and ball mills, and allows the
Charlar en Línea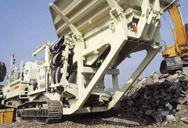
Ball Mill - an overview ScienceDirect Topics
The degree of filling the mill with balls also influences productivity of the mill and milling efficiency. With excessive filling, the rising balls collide with falling ones. Generally,
Charlar en Línea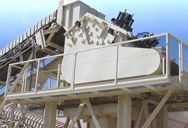
Frequency domain characterization of torque in tumbling
2018.1.1 A methodology to evaluate ball mill filling level based on torque signal is proposed. • The methodology relies on torque signal processing including spectral
Charlar en Línea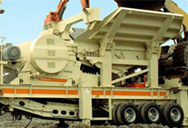
Particle filling and size effects on the ball load behaviour and
2008.10.8 The ball load behaviour in a pilot mill is studied under conditions of increasing particle filling, for coarse silica feed (0.8–1.8 mm) and fine silica feed
Charlar en Línea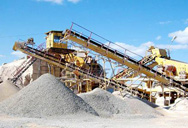
EVERY COMPONENT OF BALL MILL DETAILED
1.Axial/radial runout. 2.Alignment of the drive trains. 3.Uneven power splitting. 4.Centre distances variable. 5.Face load distribution. 6.Sealing of the girth gear. 7.Girth gear is through hardened only, fatigue strength is
Charlar en Línea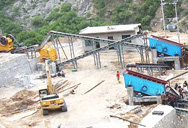
Method to Determine the Ball Filling, in Miduk Copper Concentrator SAG Mill
The results obtained from this work show, the ball filling percentage variation is between 1.2– 3.7% which is lower than mill ball filling percentage, according to the designed conditions (15%). In addition, acquired load samplings result for mill ball filling was 1.3%. Keywords: Miduk Copper oncentrator, SAG Mill, Ball Filling Percentage
Charlar en Línea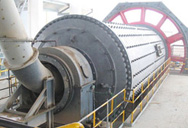
Optimization of mill performance by using online ball
Both ball and pulp shoulder angles decreased, in parallel, by about 1.5°. The ball toe angle increased by around 1°. The filling degree, computed by the Sensomag®, decreased from 31.6% to 30.9% ...
Charlar en Línea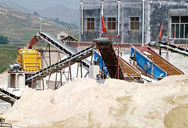
Ball Mill - On-line Estimation of In-mill Slurry Density. Bernard de ...
During the tests, the ball filling degree was kept constant in the mill, while the inlet water addition was adapted to change the slurry density in the range of [2.6 – 3.15] kg/dm³. Mill
Charlar en Línea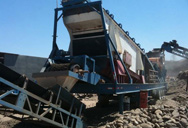
Christian Pfeiffer Ball Mill BAM for Industrial Minerals Christian ...
The BAM ball mill for industrial minerals is designed to be particularly efficient thanks to our process know-how. ... The filling level of 30 % often turns out to be the most economical nominal value. However, filling degrees around 24 – 26 % are energetically the better option for most plants, ...
Charlar en Línea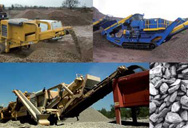
A Review of the Grinding Media in Ball Mills for Mineral
2023.10.27 The study showed that grinding media shape has a small impact on power draw when the mill filling level is low. Lameck ... found that the liberation of the locked minerals is dependent on both the mill filling rate and ball size. The liberation of the desired product in the range from 0.038 to 0.154 mm increased with ball size at ...
Charlar en Línea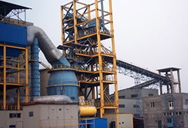
The operating principle of the ball mill
2017.2.8 Therefore, the work of the mill with partial load conditions is unprofitable. Energy consumption for ball mills is a function of many factors: the physical properties of the ground material – its specific gravity and hardness; the degree of drum filling by grinding balls; the number of drum rotations, etc. Ball mills have low efficiency ...
Charlar en Línea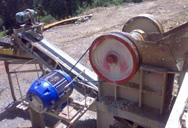
An improved method for grinding mill filling measurement and
2021.1.1 1. Introduction. Mill filling has a dominant effect on grinding mill performance (Apelt, Asprey and Thornhill, 2001), and therefore, its accurate measurement is vital for modelling grinding mill performance.Measuring filling is also necessary to estimate the composition of the load for mill modelling: rock and slurry for AG mills; rock, balls
Charlar en Línea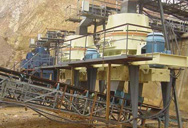
Optimisation of the secondary ball mill using an on-line ball and
2011.2.1 A total of 15 surveys were performed around the Waterval UG2 Concentrator secondary ball mill, at three different ball filling degrees and four in-mill density levels as part of optimisation studies. The filling degree and pulp level were measured using an on-line sensor called “Sensomag”, developed by Magotteaux.
Charlar en Línea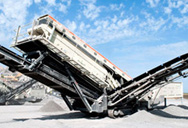
Effects of slurry filling and mill speed on the net power draw of a ...
2014.2.1 The DEM is a powerful tool to effectively explain the movement of ore particles and improve the operation, production, and efficiency of ball mills by optimizing their structure. Many researchers ...
Charlar en Línea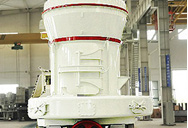
Process Training Ball Mill - INFINITY FOR CEMENT
The better mills on the market have an efficiency of about 8-9 % which means that only 8-9 % of the energy results in grinding and the majority is converted mainly into heat. The ball mill has the worst efficiency of all
Charlar en Línea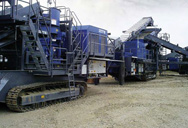
Ball charge loading - Impact of specific power ... - ResearchGate
2006.5.9 High mill filling levels were always used to put maximum energy between the trunnion bearings until the use of low filling levels initially was encouraged to prevent a failure on a dual drive ball ...
Charlar en Línea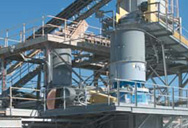
Filling ratio of vial Journal of Thermal Analysis and Calorimetry
2016.7.1 The ratio effect of total volume of balls and powders with respect to volume of vial has not been deeply considered by the researchers for ball milling process. The importance of this new parameter for ball milling process, filling ratio of vial, was investigated in this study. For this purpose, Al–Fe2O3 thermite mixture was used as the
Charlar en Línea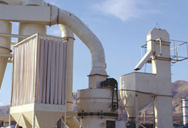
Efficiency and grinding media filling level IEEE Conference ...
2013.4.19 About 60 years ago, Fred C. Bond, George Krouse, and a few others involved in comminution research conducted some preliminary studies on low filling level of grinding media in laboratory ball mills. Initial indications were that there was a very good possibility for increased efficiency if ball mills were run with drastically reduced filling ...
Charlar en Línea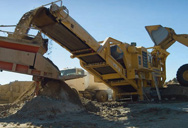
Temperature progression in a mixer ball mill - Springer
2016.4.22 Influence of the milling ball filling degree. Figure 2 illustrates the change in the temperature progression, if the milling ball filling degree Φ MB is varied. An increase of Φ MB from 0.06 to 0.36 resulted in a higher end temperature and heating rate, whereas the differences in T milling bed for 0.06 ≤ Φ MB ≤ 0.18 are small compared to
Charlar en Línea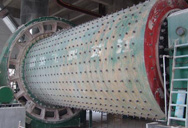
Effect of Lifter Shapes on the Mill Power in a Ball Mill
2018.12.13 The ball load behaviour in a pilot mill is studied under conditions of increasing particle filling, for coarse silica feed (0.8–1.8 mm) and fine silica feed (0.075–0.3 mm), at the mill speeds ...
Charlar en Línea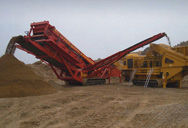
DEM Investigation of Mill Speed and Lifter Face Angle on
2018.8.7 For dry tests, the orthogonal analysis indicates that the influence order of four factors on power-mass ratio is ball filling, mill speed, powder-grinding media ratio and lifter profile and the ...
Charlar en Línea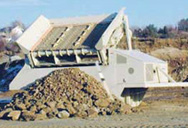
Ball mill - Wikipedia
A ball mill, a type of grinder, is a cylindrical device used in grinding (or mixing) materials like ores, chemicals, ceramic raw materials and paints. Ball mills rotate around a horizontal axis, partially filled with the material to be ground plus the grinding medium. Different materials are used as media, including ceramic balls, flint pebbles ...
Charlar en Línea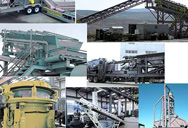
Study on the Method for Collecting Vibration Signals from Mill
2014.7.15 At present the method for measuring the fill level which used the vibration signal of mill shell shows its advantage compared with other methods. However, this method is developed late, and the technique for collecting the vibration signal from mill shell is immature. In this paper, a novel method for collecting the vibration data from mill shell
Charlar en Línea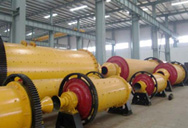
Effects of filling degree and viscosity of slurry on mill load ...
2011.10.1 Ball filling and mill fractional speed were kept constant respectively at 20% and 60% while slurry filling was varied from 0% to 300%. Using a high speed video camera, ... DEM-SPH simulation of slurry distribution in the load of a SAG mill for a viscosity of 100 mPa s and two slurry filling levels (after Cleary et al., 2006).
Charlar en Línea