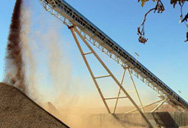
Cement - Extraction, Processing, Manufacturing Britannica
There are four stages in the manufacture of portland cement: (1) crushing and grinding the raw materials, (2) blending the materials in the correct proportions, (3) burning
Charlar en Línea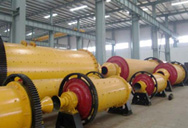
Overview of cement grinding: fundamentals, additives, technologies
2017.5.19 Abstract. Grinding is an essential operation in cement production given that it permits to obtain fine powder which reacts quickly with water, sets in few hours
Charlar en Línea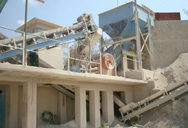
Grinding process is a critical stage in cement production
2023.8.21 Grinding process is a critical stage in cement production • Consistency: A homogeneous mixture ensures consistency in the composition of cement. It
Charlar en Línea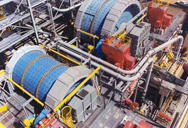
Energy-Efficient Technologies in Cement Grinding
2015.10.23 In this chapter an introduction of widely applied energy-efficient grinding technologies in cement grinding and description of the operating principles of the
Charlar en Línea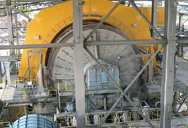
Grinding and homogenization - Al badia cement
Grinding and homogenization. The grinding process takes place in a raw mill to reduce the particle size of the components to a typical value of 10-15 % residue on a 90 um sieve.
Charlar en Línea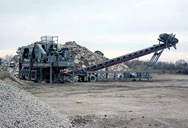
The Effect of Various Grinding Aids on the Properties of Cement
2022.1.14 Grinding aids, first introduced into cement manufacturing in 1930 , are surface-active substances that facilitate particle comminution during the milling process.
Charlar en Línea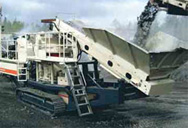
Clinker grinding technology in cement manufacturing
2019.1.3 Clinker grinding technology is the most energy-intensive process in cement manufacturing. Traditionally, it was treated as "low on technology" and "high on energy"
Charlar en Línea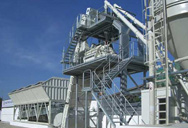
Cement Grinding Process Stages Amrit Cement
Cement Grinding Process Stages Amrit Cement. In raw grinding, a ball mill with a high efficiency separator is used to achieve uniform particle size in raw mix for the next stages
Charlar en Línea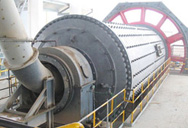
Cement grinding optimisation - ScienceDirect
2004.11.1 The electrical energy consumed in cement production is approximately 110 kWh/tonne, and around 40% of this energy is consumed for clinker grinding. There
Charlar en Línea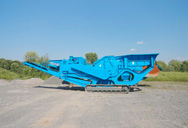
Everything you need to know about clinker/cement Grinding
Previous Post Next Post Contents Everything you need to know about clinker/cement Grinding if You read and understand this article , you will be ready to be a cement grinding area manager. FEED AND FEED SYSTEM Feed Temperature Plants with satellite coolers have high clinker temperatures: e.g. Cumarebo, Oujda.. Exit satellite cooler 200
Charlar en Línea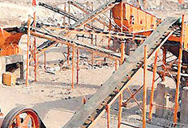
Cement - Wikipedia
Cement is seldom used on its own, but rather to bind sand and gravel ( aggregate) together. Cement mixed with fine aggregate produces mortar for masonry, or with sand and gravel, produces concrete. Concrete is the most widely used material in existence and is behind only water as the planet's most-consumed resource.
Charlar en Línea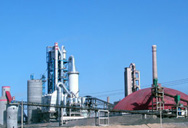
Cement Grinding - Cement manufacturing process - Priya Cement
PPC is produced by the inter-grinding and blending of 65% clinker with 30% fly ash and 5% gypsum to a fineness of 320 m 2 /kg. Fineness is a controlled parameter for cement to ensure better hydration and strength development. Ground cement is then stored in a water-proof concrete silo for packing. Particle size distribution of this cement is ...
Charlar en Línea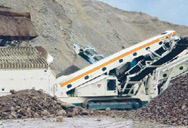
What is Concrete Grinding? - A-Core Concrete
Concrete grinding is the process of smoothing rough concrete surfaces. During the concrete grinding process, an abrasive tool with diamond attachment smooths the rough surface. All coatings, stains, and surface cracks are removed along with the top layer of concrete during the first step in the process. Deeper cracks must be evaluated.
Charlar en Línea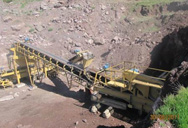
Grinding - Corrosionpedia
2018.6.13 Grinding is a subset of cutting, as grinding is a true metal-cutting process. Grinding is very common in mineral processing plants and the cement industry. Grinding is used to finish workpieces that must show high surface quality and high accuracy of shape and dimension. It has some roughing applications in which grinding removes
Charlar en Línea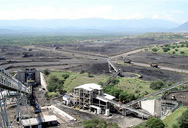
CEMENT GRINDING SYSTEMS - INFINITY FOR CEMENT EQUIPMENT
In a modern cement plant the total consumption of electrical energy is about 100 kWh/t . The cement grinding process accounts for approx. 40% if this energy consumption. Further the quality of the final cement is very dependent on the operation mode and product quality as well as consumption of electrical energy it is important that the cement ...
Charlar en Línea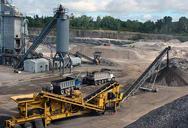
Cement Clinker Grinding Aids - 911 Metallurgist
2016.7.12 Effect of Grinding Aids on Wet Grinding. A variety of additives have been shown to have grinding aid characteristics for grinding cement clinker. Typical among these are amines, organosilicones, glycols, resins, cod oil, kojic acid, carbon blacks, wool grease, calcium sulfate, urea, asphaltenes, etc. Figure 4-26 shows a typical comparison ...
Charlar en Línea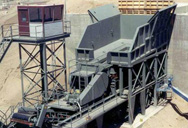
Portland cement - Wikipedia
Cement grinding A 10 MW cement mill, producing cement at 270 tonnes per hour. To achieve the desired setting qualities in the finished product, a quantity (2–8%, but typically 5%) of calcium sulfate (usually gypsum or anhydrite) is added to the clinker, and the mixture is finely ground to form the finished cement powder. This ...
Charlar en Línea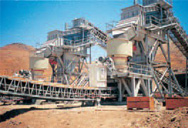
Mutual compatibility of superplasticizers (PC, SNF), grinding aids
2023.4.10 The compatibility of grinding aids (TEA/glycol) and superplasticizers (PC/SNF) in low- and high-C 3 A cements, as well their mutual effect on the properties of pastes and fresh/hardened mortars were evaluated. The influence of various surfactant combinations on the hydration rate, flowability, compressive strength, rheology, surface
Charlar en Línea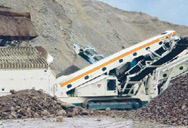
What is Concrete Grinding? - A-Core Concrete
Concrete grinding is the process of smoothing rough concrete surfaces. During the concrete grinding process, an abrasive tool with diamond attachment smooths the rough surface. All coatings, stains, and surface cracks are removed along with the top layer of concrete during the first step in the process. Deeper cracks must be evaluated.
Charlar en Línea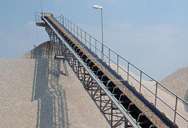
(PDF) Grinding in Ball Mills: Modeling and Process Control
2012.6.1 A ball mill is a type of grinder widely utilized in the process of mechanochemical catalytic degradation. It consists of one or more rotating cylinders partially filled with grinding balls (made ...
Charlar en Línea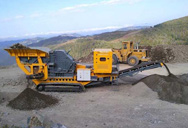
Cement Grinding - Cement Plant Optimization
Grinding aids also serve to reduce coating problems in cement storage and enhances cement strengths. GRINDING MILLS. Mills will be selected according to type most suitable for required capacity and duty and for overall power consumption. Cement grinding operation may be performed in one of the following mill setups. Ball and tube mills.
Charlar en Línea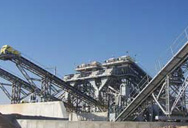
Investigation on grinding impact of fly ash particles and its ...
2019.6.1 In grinding process, the quality of cement in terms of fineness was measured by using Blaine's surface area and particle size distribution analysis [18]. The ball milled powder particles having the non-spherical shape, changes in physical characteristics only and no alteration in chemical composition of a particle [19], [20].
Charlar en Línea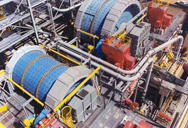
Journal of Physics: Conference Series PAPER OPEN ACCESS You
in cement grinding. Grinding aids are active surface agents that counteract the agglomeration of very fine particles on the grinding media, thus inhibiting the grinding effect and therefore reducing production rates. A number of grinding aids ar e available on the market. The most suita ble grinding aid for a certain grinding
Charlar en Línea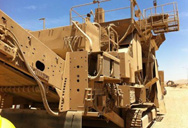
Vertical roller mill - Wikipedia
The vertical roller mill is a kind of grinding machine for cement, raw material, cement clinker, slag and coal slag. It has the benefits of simple structure and low cost of manufacture and use. Vertical roller mills have many different forms, but they work basically the same. All of these forms come with a roller (or the equivalent of roller ...
Charlar en Línea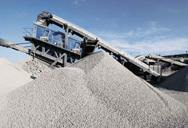
Cement Clinker Calcination in Cement Production Process AGICO Cement
The cement production processes mainly include raw material crushing and storage, raw material proportioning and grinding, clinker calcination, clinker grinding, cement packing, etc. Portland cement is the most widely used cement in our daily life. It is made from a variety of raw materials, typically sand, iron ore, clay, gypsum, limestone ...
Charlar en Línea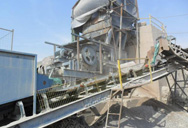
What is a cement grinding unit and what processes are involved
2023.3.14 A cement grinding unit is a facility that is used to grind clinker (a hard nodular material produced by sintering aluminosilicate and limestone) into a fine powder, known as cement. The process of ...
Charlar en Línea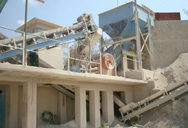
Role of Gypsum in Cement and its Effects - The Constructor
In the manufacture process of cement, clinkers are formed. These cement clinkers are cooled down and added with small amount of gypsum. The mixture then sent to final grinding process. For ordinary Portland cement it remains between 3 to 4% and in case of Quick setting cement it can be reduced up to 2.5%. Role of Gypsum in Cement
Charlar en Línea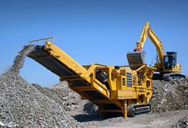
2 Major Roles of Limestone in Cement Manufacturing
2023.5.27 Cement grinding can be carried out either in an integrated cement plant or in a stand-alone cement grinding station. 3. What should limestone be mixed with to make cement? This needs to start with the cement composition. Cement is made through a tightly controlled chemical combination of calcium, silicon, aluminum, iron, and other
Charlar en Línea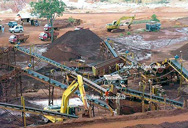
How does a raw mill work in a cement plant? - LinkedIn
2022.12.19 Cement raw mills typically include a hopper, which feeds material into the mill, grinding elements such as rollers or balls, a separator, and a drive system for rotating the rollers or balls.
Charlar en Línea