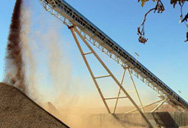
The six main steps of iron ore processing - Multotec
Six steps to process iron ore 1. Screening. We recommend that you begin by screening the iron ore to separate fine particles below the crusher’s CSS... 2. Crushing and stock piling. This step involves breaking up the iron ore to obtain an F 80 grind size before it can be...
Charlar en Línea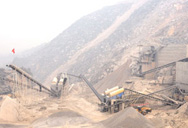
Crushing characteristics and performance evaluation of iron ore in
2023.12.1 In this study, the crushing process of spherical iron ore particles, constructed by an Apollonian sphere packing (ASP) method, was numerically
Charlar en Línea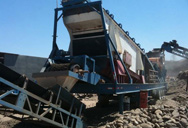
(PDF) SIZE REDUCTION BY CRUSHING METHODS
2017.3.4 SIZE REDUCTION BY CRUSHING METHODS Authors: A. Balasubramanian University of Mysore Abstract and Figures In the field
Charlar en Línea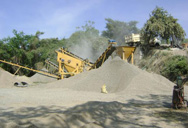
Iron processing Definition, History, Steps, Uses, Facts
iron processing, use of a smelting process to turn the ore into a form from which products can be fashioned. Included in this article also is a discussion of the mining of iron and of its preparation for smelting. Iron (Fe) is a
Charlar en Línea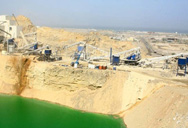
Crushing Circuit - an overview ScienceDirect Topics
The first step of physical beneficiation is crushing and grinding the iron ore to its liberation size, the maximum size where individual particles of gangue are separated from the iron
Charlar en Línea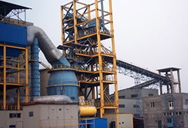
Iron Ore Processing, General SpringerLink
2022.10.20 Making iron and steel from iron ore requires a long process of mining, crushing, separating, concentrating, mixing, agglomeration (sintering and
Charlar en Línea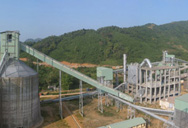
A Mine-to-Crusher Model to Minimize Costs at a
2022.8.18 This paper presents an economic analysis of a mine-to-crusher model to estimate and minimize the operating expenses of an open-pit iron mine located in northern Brazil. The activities at this truckless
Charlar en Línea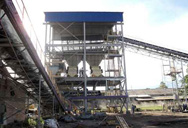
Iron Ore Processing, General
Making iron and steel from iron ore requires a long process of mining, crushing, separating, concentrating, mixing, agglomeration (sintering and pelletizing), and shipping
Charlar en Línea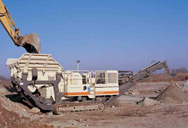
Iron Mining Process - Minnesota Iron
Iron Mining Process. From blasting to crushing to separation – more than 85% of the iron mined in the United States is mined in northeastern Minnesota to make our nation’s steel. Blasting. Taconite is a very hard
Charlar en Línea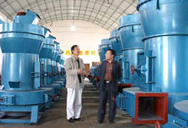
Research into the crushing and grinding processes of iron ore with
1 Introduction. The effectiveness of simultaneous effect of mechanical load and electric field of ultra-high frequency (UHF) in the process of iron ore crushing is substantiated in
Charlar en Línea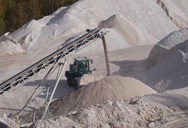
A Mine-to-Crusher Model to Minimize Costs at a
2022.8.18 In the main configuration available to the truckless system, the mining method consists of drilling, blasting, loading (done by a shovel, which delivers material directly onto an in-pit conveying system for
Charlar en Línea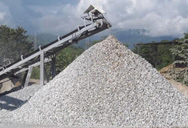
Processing and Reusing Technologies for Steelmaking Slag
The iron/steel slag processing flow is schematically shown in Fig. 2. Steelmaking slag is subjected to the following four process-es: ① solidify and cooling of the hot molten slag, ② crushing and magnetic separation treatment of the slag to recover the metal iron, ③ crushing and classification of the slag for grain size adjustment
Charlar en Línea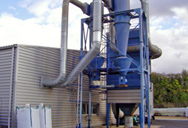
Beneficiation process and separation method,crushing
2020.9.17 Beneficiation process and separation method. 09-17-20; 1,255 Views; icon 0 . Beneficiation process and separation method . Crushing: The process of breaking the ore blocks with a particle size of 500-1500mm from
Charlar en Línea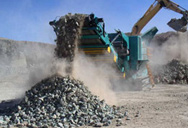
How to Recover Iron from Magnetite: 4 Methods and Stages
2023.4.7 Stage 4 Magnetite dehydration. Since the iron concentrate after separation contains some water, dehydration treatment is required. 1 The separated iron concentrate slurry flows into the thickener for sedimentation to remove a large amount of water. 2 After drying and dehydration in a dryer, the dried iron concentrate powder is obtained.
Charlar en Línea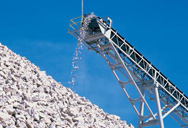
Iron processing - Ores, Smelting, Refining Britannica
Iron processing - Ores, Smelting, Refining: Iron ores occur in igneous, metamorphic (transformed), or sedimentary rocks in a variety of geologic environments. Most are sedimentary, but many have been changed by weathering, and so their precise origin is difficult to determine. The most widely distributed iron-bearing minerals are oxides, and
Charlar en Línea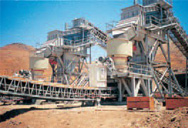
Processing the ores of rare-earth elements MRS Bulletin
2022.3.21 Rare-earth elements (REEs) are required for use in modern high-tech applications and demand has increased significantly over the last decade. 1 However, processing of REE ores poses potential hazards to human health and the environment due to challenges in the management of thorium (Th) and uranium (U) in waste products. 2 If
Charlar en Línea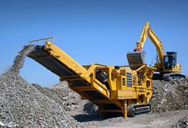
Processes for Beneficiation of Iron Ores – IspatGuru
2015.3.28 The term beneficiation in regard to iron ores encompasses all of the methods used to process ore to improve its chemical, physical and metallurgical characteristics in ways which makes it a more desirable feed for the iron making furnace. Such methods include crushing and grinding, washing, filtration, sorting, sizing, gravity
Charlar en Línea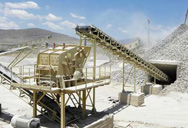
Ore Processing Multotec
To achieve this, ore processing separates the different mineral characteristics using various ore dressing (ore processing) methods. The primary processes are crushing and grinding of ore, ore sizing and separation. To separate the ore into applicable sizes for further processing, screening, classifying, concentration separation, heavy medium ...
Charlar en Línea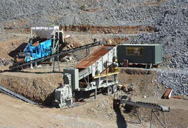
OVERVIEW OF MINERAL PROCESSING METHODS - ResearchGate
3 2.0 Major Processes of Mineral processing: The following are the major processing methods involved in ore dressing/ mineral processing: 1. Size reduction (Crushing ,Grinding ) 2.
Charlar en Línea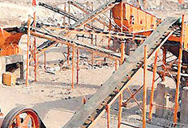
Recent Advancements in Metallurgical Processing of Marine Minerals
2021.12.19 3. Processing of Marine Minerals. Processing involves separating an ore from a waste and transforming it into a product (e.g., metal). The number and type of steps involved in a particular process may vary significantly depending on the physical, chemical, and mineralogical properties of the processed ore.
Charlar en Línea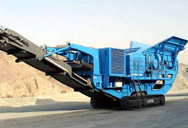
SIZE REDUCTION BY CRUSHING METHODS By - ResearchGate
Crushing is the largest process operation in minerals processing. The goal is to produce rock or (more seldom) mineral fractions to be used as rock fill or ballast material for concrete and asphalt
Charlar en Línea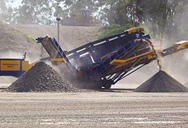
Cracking and Microstructure Transition of Iron Ore
2023.3.22 The phenomenon of cracking and deterioration of iron ore particles is a widespread scientific problem in the field of mineral processing and metallurgy. In this paper, the thermal decomposition
Charlar en Línea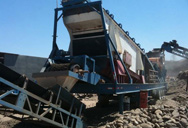
Iron processing - Smelting, Refining, Alloying
Iron processing - Smelting, Refining, Alloying: The primary objective of iron making is to release iron from chemical combination with oxygen, and, since the blast furnace is much the most efficient process, it receives the
Charlar en Línea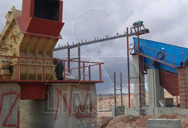
Iron Ore Processing,Crushing,Grinding Plant Machine
Iron ore is the key raw material for steel production enterprises. Generally, iron ore with a grade of less than 50% needs to be processed before smelting and utilization. After crushing, grinding, magnetic separation, flotation, and gravity separation, etc., iron is gradually selected from the natural iron ore.
Charlar en Línea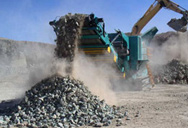
Beneficiation of Iron Ores – IspatGuru
2014.4.3 Fig 3 Types of processing ores. The wet processing (Fig 4) is normally practiced for low / medium grade (60 % Fe to 63 % Fe) hematite iron ore. The wet process consists of multi-stage crushing followed by different stages of washing in the form of scrubbing and / or screening, and classification etc., but the advantage is only partial
Charlar en Línea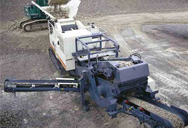
Process simulations in mineralogy-based geometallurgy of iron
Geometallurgy utilises geological and mineral processing information to capture the spatial metallurgical characteristics of the ore body. Mineralogy-based geometallurgical modelling employs quantitative mineralogical information, both on the deposit and in the process. The geological model must describe the minerals present, give their ...
Charlar en Línea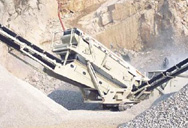
(PDF) Beneficiation and flowsheet development of a low grade iron
2020.12.1 According to the results a flowsheet was developed. From the developed flowsheet, it is possible to obtain pellet grade concentrate with 65.41% Fe, 2.54% SiO2, 2.79% MgO, 0.70% CaO and 0.32% Al2O3 ...
Charlar en Línea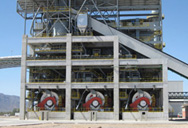
Extraction of Iron, Iron Mining, Iron Ore Processing
Different siderite has different iron ore processing methods. The extraction of iron from single siderite with coarse grain size is suitable to be treated with single gravity separation, ... Strong magnetic separation: two-and-half-block close circuit crushing and screening + strong magnetic separation.
Charlar en Línea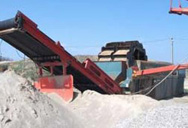
From mine to port - LKAB
The road from mine to steel is a long journey that begins with exploration, which involves testing the bedrock for mineral deposits. If exploration is successful, mining and processing can follow. Our main products from the mines are iron ore pellets and fines, which are transported by rail to our ports in Luleå and Narvik and then shipped ...
Charlar en Línea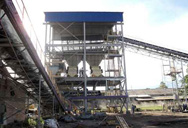
Crushing Screening Plant - 911 Metallurgist
2016.7.12 Crushing Screening Plant. Methods used in Crushing Screening Plants on ore range from a simple combination of a grizzly and one crusher to an elaborate arrangement in series of grizzly, jaw crusher, screens, and rolls or cone crushers. Crushing is done underground at a few large mines. In general, the jaw crusher is the most suitable ...
Charlar en Línea