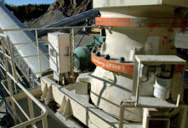
Raw Mill, Cement Raw Mill, Raw Mill In Cement Plant Cement
In the cement manufacturing process, raw mill in cement plant grind cement raw materials into the raw mix, and the raw mix is sent to the cement kiln to make cement
Charlar en Línea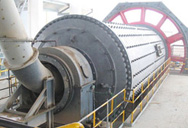
Cement Production Process Cement Manufacturing Process
2020.8.25 How much do you know about cement production process? A full cement production process includes the cement crushing process, raw mill process, clinker
Charlar en Línea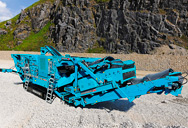
The cement mill
Cement clinker is usually ground using a ball mill. This is essentially a large rotating drum containing grinding media - normally steel balls. As the drum rotates, the motion of the
Charlar en Línea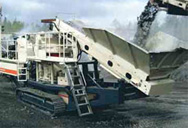
Advanced process control for the cement industry - FLSmidth
get the most out of its cement plant, Expert Control and Supervision (ECS) is the key. FLSmidth’s ECS/ProcessExpert provides advanced process control and optimization for
Charlar en Línea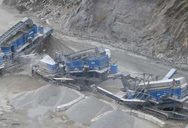
How Cement is Made - Cement Manufacturing Process
Stage 1: Raw Material Extraction/Quarry. The raw cement ingredients needed for cement production are limestone (calcium), sand and clay (silicon, aluminum, iron), shale, fly
Charlar en Línea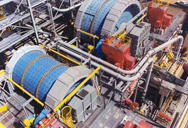
In the heart of the process of cement manufacturing (English
2019.8.27 13K views 1 year ago. This 3D visit explains, in 6'30'', the full cycle of the process of cement manufacturing, highlighting its technical and environmental specifities.
Charlar en Línea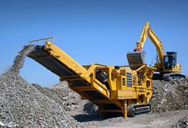
Optimization of Cement Manufacturing Process
1987.8.1 Cement manufacturing process is now operated with the aid of various control systems, such as raw meal composition control, kiln control and mill control.
Charlar en Línea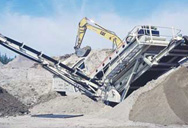
Modeling of energy consumption factors for an industrial cement ...
2022.5.9 Cement production is one of the most energy-intensive manufacturing industries, and the milling circuit of cement plants consumes around 4% of a year's
Charlar en Línea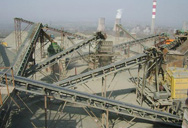
Cement Mill Cement Ball Mill Vertical Cement Mill AGICO
Cement mill is the core equipment for grinding material after clinker production. Generally, the cement mill can be called cement grinding mill. Among production cost of cement
Charlar en Línea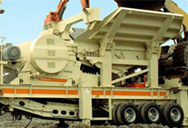
How Is Cement Produced in Cement Plants Cement Making Process
Generally, the proportion of components in cement raw materials is 67-75% limestone, 10-15% clay, 0.5-1.5% iron ore and 8.5-11% coal. The laboratory of a cement plant. With the help of vertical roller mills or other types of crushers, the raw materials are blended and further ground into smaller pieces of raw meal in the cement plant.
Charlar en Línea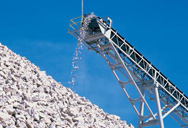
Cement - Extraction, Processing, Manufacturing Britannica
There are four stages in the manufacture of portland cement: (1) crushing and grinding the raw materials, (2) blending the materials in the correct proportions, (3) burning the prepared mix in a kiln, and (4) grinding the burned product, known as “ clinker ,” together with some 5 percent of gypsum (to control the time of set of the cement).
Charlar en Línea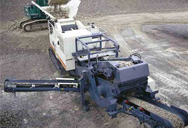
Cement Plant, Cement Equipment - Cement Manufacturing Process
2020.1.27 6 steps of the cement manufacturing process. When we talked about the manufacturing of cement, anyone who knows the cement manufacturing process slightly will mention “two grinding and one calcination”, they are namely: cement raw material preparation, clinker production, and cement grinding. In the real cement production line,
Charlar en Línea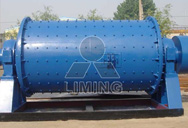
BASIC CEMENT PLANT LAYOUT – Process Cement Forum - The Cement
2020.2.3 14 Cement Mill and Bag House . Clinker, along with additives, is ground in a cement mill. The output of a cement mill is the final product viz. Cement. In a cement mill, there is a cylindrical shell lying horizontal which contains metallic balls and as it rotates, the crushing action of the balls helps in grinding the clinker to a fine powder.
Charlar en Línea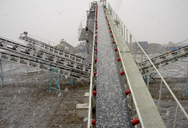
The 6 Main Process Fans in Cement factory
Raw mill exhaust fans or stack fans are also called as de-dusting fans. In cement industry raw mill exhaust fans handle 2.2 ton of exhaust gases for the production of 1 ton of clinker. Raw mill exhaust fans are operated with very adverse situations because the fan handles mainly gases such as CO2, N2, NOx and Sox along with some dust particles.
Charlar en Línea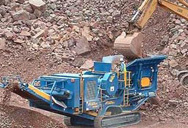
cement plant calculations kiln, mills, quality, combustion, etc. all ...
Cement C3S, C2S, C3A, C4AF. Burnability index (for clinker) Burnability factor (for clinker) Burning temperature (minimum) Go To Online Calculators. 28-days mortar strength Mpa. Gypsum Set Point (GSP) Go To Online Calculators. False air calculations, heat loss calculations, LSF, Silica modulus, alumina modulus, calorific value, minimum ...
Charlar en Línea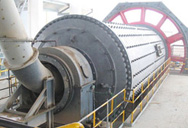
PROCESS TRAINING for operators of Vertical RAW Mills
For company control matters and for the training of the operators it is helpful to note down the process parameters in a log book every hour. Beside start – stop time and any problems in the grinding plant the following parameters are recommended for being entered the log sheet: -feed rate to the mill, production rate (t/h]
Charlar en Línea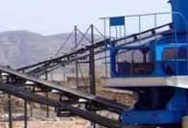
Energetic and exergetic assessment of a trass mill process in a cement
2009.9.1 Energetic and exergetic assessment of a trass mill process in a cement plant. Cement production has become one of the most intensive energy industries in the world. For producing it, addition materials have been widely used in cement factories. The main objective of this study is to assess the performance of a trass mill in a cement
Charlar en Línea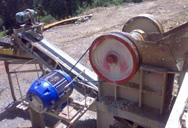
Optimization of Cement Manufacturing Process - ScienceDirect
1987.8.1 Tokyo. Japan 1986 OPTIMIZATION OF CEMENT MANUFACTURING PROCESS G. Nakamura, T. Aizawa and K. Nakase Onoda Cement Co., Ltd., 1-1-7, Toyosu Koto-ku, Tokyo,japan Abstract. Cement manufacturing process is now operated with the aid of various control systems, such as raw meal compositi on control, kiln control and mill
Charlar en Línea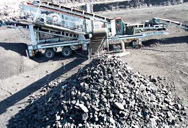
Process Training Ball Mill - INFINITY FOR CEMENT EQUIPMENT
Process Training Ball Mill. To Download this post + all manuals and books and Excel sheets and all notes I collected over my 23 years of experience in Cement industry click here now INTRODUCTION. Comminution is a major unit operation in a cement plant, accounting for about 50- 75 % of the total plant energy consumption.
Charlar en Línea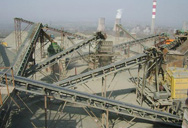
What Are the Parts of a Cement Mills? - Cement Ball Mill Production Process
2023.8.23 A cement mill is a fundamental component of the cement manufacturing process, playing a vital role in breaking down and grinding cement clinker into fine powder. This finely ground powder, when mixed with other materials, produces the building material we commonly know as cement. To achieve this crucial transformation, a cement mill
Charlar en Línea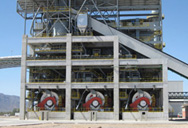
Energy and cement quality optimization of a cement grinding circuit
2018.7.1 Energy optimization of a circuit has been subject of many of the studies. Jankovic et al. [12] considered the optimization alternatives of cement grinding circuits. Benzer [13] studied on optimizing the fully air-swept raw mill grinding circuit, Dundar et al. [14] reported the optimization opportunities of a cement grinding circuit.
Charlar en Línea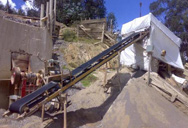
Cement Mill Cement Ball Mill Vertical Cement Mill AGICO
Cement mill in cement plant. Cement mill is the core equipment for grinding material after clinker production. Generally, ... For a complete project: the material availability, the required output capacity, the process technology, your budgetary and financing status, the estimated starting time, etc. For singular machinery: the model, ...
Charlar en Línea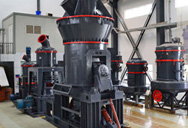
Cement Grinding Unit Cement Grinding Plant Cement
Cement grinding unit cost. Take the annual output of 600,000 tons of large-scale cement grinding station as an example, there are three common options can be recommended: SCHEME 1: roller press + φ 3.2 ×13m ball mill; SCHEME 2: φ 3.8 ×13m closed mill; SCHEME 3: clinker fine crusher + cement roller press+φ 3.2 ×13m ball mill.
Charlar en Línea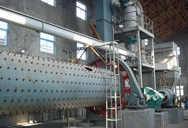
Cement Plant: The Manufacturing Process 4 5
Cement Plant: The Manufacturing Process worldcementassociation 1 Limestone (CaCO3) is taken from a quarry 2 4 3 The limestone is fed into a crusher and then stored until needed The clinker is mixed with additives, such as gypsum, and then ground in a cement mill, which creates cement The cement is then packed and distributed to
Charlar en Línea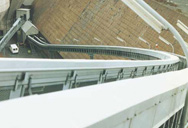
Energetic and exergetic assessment of a trass mill process in a cement
2009.9.1 The trass mill in a cement production plant has been investigated in relation to exergy analysis. The objective of S € o güt et al. [18] was to perform an energetic and exergetic assessment of ...
Charlar en Línea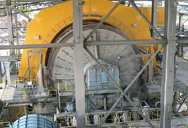
(PDF) Thermodynamic Analysis of Raw Mill in Cement Industry
The process model is based on a raw mill plant operation with capacity of 240,000 kg per hour, and includes the required physical property parameters to simulate this type of system. The raw mill process consists of three-unit operations, namely:
Charlar en Línea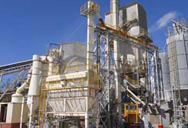
Mini Cement Plant, Small Cement Plant 50-1000TPH EPC Cement Plant
Plant Capacity: 50 MT/Day. Plant Machinery: about 117155 dollars. Working Capital: about 103208 dollars. Total Capital Investment: about 348675 dollars. Return: 23.00%. Break Even: 63.00%. Start Your Mini Cement Plant!
Charlar en Línea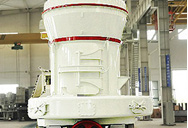
Advanced process control for the cement industry - FLSmidth
FLSmidth – the process knowledge experts FLSmidth’s international team of process experts designs solutions specifically for cement applications. With more than 40 years of plant automation experience, FLSmidth has installed over 700 control systems and 450 laboratory systems – and understands the needs of today’s cement plants.
Charlar en Línea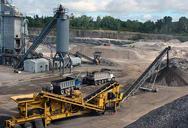
Cement Grinding Plant Overview Cement Grinding Unit AGICO Cement
2019.10.11 As a cement grinding plant manufacturer, AGICO Cement can provide a cement EPC project as you need. We have rich experience in design cement plants and process cement manufacturing machines, such as cement crusher, cement ball mill, cement vertical mill, cement roller press, cement kiln, dryer, clinker cooler, and related
Charlar en Línea