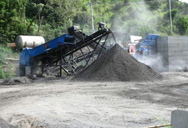
The six main steps of iron ore processing - Multotec
Six steps to process iron ore 1. Screening We recommend that you begin by screening the iron ore to separate fine particles below the crusher’s CSS before the crushing stage. A static screen is used to divert the fine particles for crushing. This step prevents
Charlar en Línea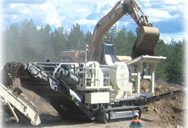
Iron Ore production in the Pilbara
Processing of the ore ranges from simple crushing and screening to a standard size, through to processes that beneficiate or upgrade the quality of the iron ore products.
Charlar en Línea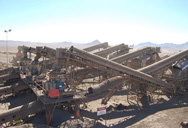
Flow chart of the mineral processing of hematite iron ore.
Flow chart of the mineral processing of hematite iron ore. Source publication An intelligent factory-wide optimal operation system for continuous production process
Charlar en Línea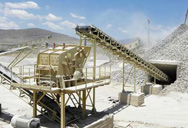
Iron Ore Processing, General SpringerLink
2022.10.20 Making iron and steel from iron ore requires a long process of mining, crushing, separating, concentrating, mixing, agglomeration (sintering and pelletizing),
Charlar en Línea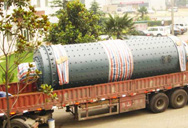
Iron Ore Processing, General
Iron Ore Processing, General 1 Introduction Iron is the world’s most commonly used metal–steel, of which iron ore is the key ingredient, representing almost 95% of all metal
Charlar en Línea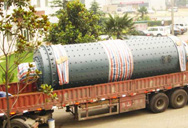
Iron Ore Characterization Techniques in Mineral Processing
2023.4.27 well as ore processing. Keywords Iron ore Characterization SEM–EDS XRD XRF FTIR Introduction The most common element that makes up
Charlar en Línea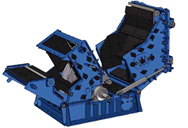
Life cycle assessment of iron ore mining and processing
2015.1.1 The study used typical iron ore mining and processing operations in Pilbara, Western Australia, as a case study and covers the upstream part of the cradle-to
Charlar en Línea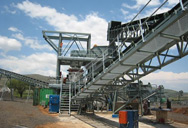
Iron ore mining and dressing - tec-science
2018.6.21 The flow chart shows the basic steps of how iron ore is used to produce semi-finished products of steel. The individual process steps are explained in more detail in the following articles. Figure: From
Charlar en Línea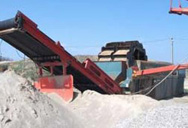
Iron Ore production in the Pilbara
Ore car dumping Once the train arrives at the port the ore cars go through the car-dumper. The ore cars are rotated and the ore flows out into bins and then is discharged onto conveyors. Stockpile The ore is stockpiled according to product type and the quality control plan. The travelling stackers create 250m long stockpiles. Rotary bucket-wheel
Charlar en Línea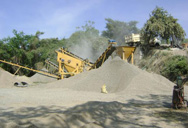
Iron processing Definition, History, Steps, Uses, Facts
iron processing, use of a smelting process to turn the ore into a form from which products can be fashioned. Included in this article also is a discussion of the mining of iron and of its preparation for smelting. Iron (Fe) is a
Charlar en Línea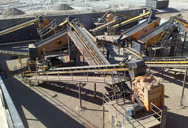
Simplified flow chart showing typical iron ore
Download scientific diagram Simplified flow chart showing typical iron ore processing (Silva et al., 2021). from publication: Behavioural analysis of iron ore tailings through critical state ...
Charlar en Línea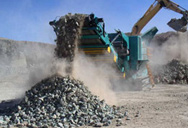
Iron Ore Processing - an overview ScienceDirect Topics
In India, where iron ore processing is one of the major industries, the generation of tailings is estimated to be 10-25 % of the total iron ore mined, amounting to 18 million tons per year (Das et al., 2000 ). The tailings contain silica in high percentage (40-60 %, from various locations). This makes it a suitable raw material for the ...
Charlar en Línea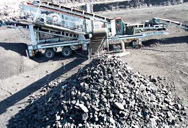
Iron Ore Characterization Techniques in Mineral Processing
2023.4.27 While iron is a pivotal metal that is exploited commercially, its extraction from ores, subsequent processing and purification follows a series of steps, and material characterization in terms of physical, chemical and mineralogical features and behavior is imperative at each stage. Some characterization tests rely solely on physical
Charlar en Línea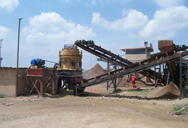
Characterization and Beneficiation of Dry Iron Ore Processing
fine ore having size below 8 –10 mm. Dry processing of iron ore is popular for treating hard massive hematitic ores; however, fines generated during processing of goethite-rich mineral cause significant quantity loss of iron values in rejects and make the process inefficient. During dry processing of iron ore in
Charlar en Línea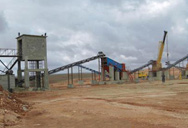
Iron Ore Pelletizing Process: An Overview - IntechOpen
Evolution of binders for iron ore pelletizing Induration technologies Challenges and innovations in iron ore pelletizing 2. Pelletizing process and raw materials The iron ore is mined mostly from open pit deposits through mining operations and the raw product, run of mine, is subjected to mineral processing.
Charlar en Línea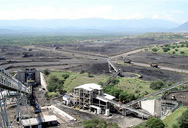
Process flow diagram of Chadormalu Iron ore concentrator plant.
For iron ores with significant amounts of rare-earths [47,[320][321][322][323] [324] [325], the incorporation of rare-earth recovery steps can improve the economy of the ore beneficiation process ...
Charlar en Línea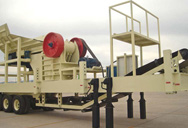
Extraction of Iron Metallurgy Blast Furnace and Reactions
It’s a long process which begins with Concentration through calcination roasting. Concentration removes the water and other volatile impurities such as sulphur and carbonates. This concentrated ore is mixed with limestone (CaCO 3) and Coke and fed into the blast furnace from the top. It is in the blast furnace that extraction of iron occurs.
Charlar en Línea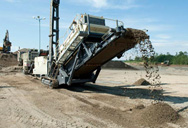
How to create mineral processing and mining flowcharts in Excel
2023.5.18 Left click on the Insert tab to insert the provided-icon in the Worksheet Window or the canvas. There are not many mining type provided-icons in Excel. Figure 3 A cart icon, an example of a mining ...
Charlar en Línea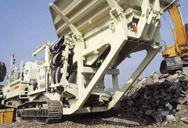
Iron Ore Processing, General SpringerLink
2022.10.20 Iron ore handling, which may account for 20–50% of the total delivered cost of raw materials, covers the processes of transportation, storage, feeding, and washing of the ore en route to or during its various stages of treatment in the mill.. Since the physical state of iron ores in situ may range from friable, or even sandy materials, to monolithic
Charlar en Línea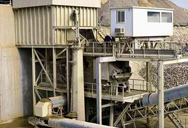
(PDF) Beneficiation and flowsheet development of a
2020.12.1 In the present study a detailed characterization followed by beneficiation of low grade iron ore was studied. The Run of Mine (R.O.M) sample assayed 21.91 % Fe, which is very low grade in nature.
Charlar en Línea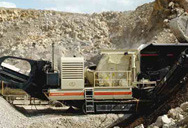
Mineral processing - Wikipedia
Mineral processing can involve four general types of unit operation: 1) Comminution – particle size reduction; 2) Sizing – separation of particle sizes by screening or classification; 3) Concentration by taking advantage of physical and surface chemical properties; and 4) Dewatering – solid/liquid separation. In all of these processes ...
Charlar en Línea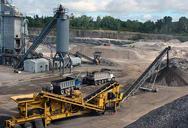
Iron Ore: From Mining to Processing to Dust Control
Iron ore is a rock or mineral from which metallic iron can be extracted economically. It constitutes 5% of the earth’s crust. Viable forms of ore contain between 25% and 60% iron. Ore greater than 60% iron is known as natural ore or direct shipping ore, meaning it can be fed directly into iron-making blast furnaces.
Charlar en Línea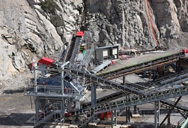
Coal Processing - Multotec
Coal Processing Flow Chart: Coal Beneficiation Benefits From Multotec. Coal beneficiation machinery from Multotec enables you to achieve your processing goals at the lowest cost per ton. ... Thermal coal is used in energy generation for heating and metallurgical coal is primarily mixed with iron ore to produce steel.
Charlar en Línea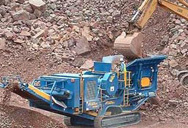
Processing Equipment Flow Chart Cases - JXSC Mining
Solution Mining: Solution mining can substitute for conventional shaft mining in potash deposits that occur below 3,000 feet. Vertical pipes are drilled to supply water to the ore zone and a return pipe brings the saturated brine to the surface where it is evaporated in surface ponds leaving potash.
Charlar en Línea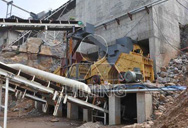
Iron Ore Processing
Iron Ore Processing 504. 6 Wet H igh Intensity M agnetic S eparation of cyclone underflow The cyclone under -flow obtained from hydrocycloning condition was further treated in wet high intensity magnetic separator at current of 0.6Amp . The results obtained are presented in Fig. 4. M agnetic fraction ...
Charlar en Línea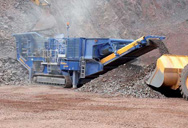
Iron ore beneficiation: an overview - ScienceDirect
2023.1.1 Processing of low-grade ore. Flow-sheets for low-grade ore processing of different iron ore mines vary significantly; however, the underlying principle of operation is very similar. Methodology for selection of beneficiation flowsheet is already defined in the above sections. For beneficiation of coarser fraction (+1 mm), jigging is widely used.
Charlar en Línea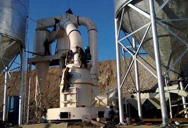
Mineral Processing Flowsheets - 911 Metallurgist
2016.3.8 The Mineral Processing Flowsheets shown on the following pages are based on actual data obtained from successful operating plants. Metallurgical data are shown in these flowsheets which incorporate Crushers, Grinding Mills, Flotation Machines, Unit Flotation Cells, and Selective Mineral Jigs as well as other standard milling equipment.
Charlar en Línea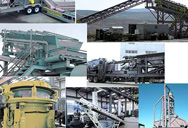
Iron ore - Wikipedia
Iron ores are rocks and ... The addition of 1% can double the distance molten iron will flow. The maximum effect, about 500 °C (932 °F), ... Iron Ore Price and Historical Chart; Iron Mines of NY/NJ; Iron ore capacity by major world producer This page was last edited on ...
Charlar en Línea