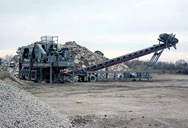
Clinker Production - Clinker Manufacturing - Cement Plant
We are a trustworthy partner! Clinker production can be divided into preheating and pre-calcining, clinker sintering, and clinker cooling three stages. Cyclone preheater, cement kiln, and clinker cooler are three main cement manufacturing machines in this process.
Charlar en Línea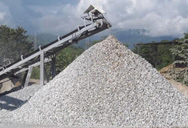
Cement and Clinker Production by Indirect Mechanosynthesis
2022.9.21 The cement and clinker produced by indirect mechanosynthesis (15 min of mechanical activation and heat treatment 900 C or 1200 C) were characterized. In
Charlar en Línea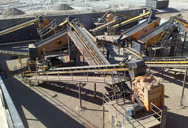
Cement Clinker Production - an overview ScienceDirect
This chapter has assessed the use of MIBA as both an aggregate component and, after grinding, a cement component, in a range of concrete-related applications, including
Charlar en Línea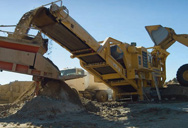
Clinker Plant Cement Plant Cement Equipment For Clinker Production
2019.12.2 Clinker plant is applied to clinker production, we can classify the clinker plant into two parts, preheat and precalcining, burning in the rotary kiln. AGICO Cement is a cement plant manufacturer with rich experience, and we are specialized in cement plant and cement equipment. Based on rich experience and advanced technology support,
Charlar en Línea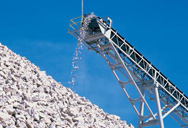
Cement - Extraction, Processing, Manufacturing Britannica
There are four stages in the manufacture of portland cement: (1) crushing and grinding the raw materials, (2) blending the materials in the correct proportions, (3) burning the prepared mix in a kiln, and (4) grinding the burned product, known as “ clinker ,” together with some 5 percent of gypsum (to control the time of set of the cement).
Charlar en Línea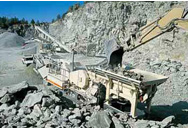
Cement Manufacturing Process - INFINITY FOR
Clinker production is the most energy-intensive stage in cement production, accounting for over 90% of total industry energy use. Clinker is produced by pyro-processing in kilns. These kiln systems evaporate the
Charlar en Línea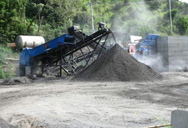
Large Cement Plant for Sale
In contrast to mini cement plants, we usually call the cement plant with a clinker production capacity of more than 2,500 TPD as the large cement plant.. As a manufacturer who specializes in cement technology development and equipment upgrading and has over decades of cement machinery manufacturing experience,
Charlar en Línea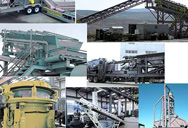
Cement Equipment In Cement Plant AGICO Cement Plant
Cement Equipment Supplier. AGICO Cement is located in Henan, China. It was founded in 1997 with a registered capital of 81.34 million yuan. It covers an area of 660000m 2 which includes a construction area of 30000 m 2. In 2004, AGICO passed the ISO9001 certification and enjoyed the self-management right of import and export.
Charlar en Línea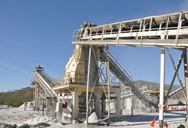
Cement processing equipment Schenck Process
Weighbridge for Rail Loading of Cement. At a glance: feeding alternative fuels in Cement. Schenck Process alternative fuel PSP handling and feeding system provides a reliable and trusted processing solution for a UK cement plant. LOGiQ® - Customer-centric digital solutions by Schenck Process.
Charlar en Línea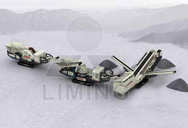
Energy-Efficient Technologies in Cement Grinding IntechOpen
2015.10.23 In this chapter an introduction of widely applied energy-efficient grinding technologies in cement grinding and description of the operating principles of the related equipments and comparisons over each other in terms of grinding efficiency, specific energy consumption, production capacity and cement quality are given. A case study
Charlar en Línea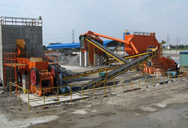
Cement Machinery - Cement Making Machine Latest Price,
Tilting drum mixer diesel engine cement kalavai machine, for... Cement manual bag feeding machine, capacity: 20 ton - 25 ton; Automatic cement plant, capacity: 100 tpd to 3500 tpd; Cement plant machinery; 50 hp to 1200 hp mild steel ball mill balls, for chemical in... Cement spreader machine; 10-800 hp mild steel wet ball mill, fly ash brick ...
Charlar en Línea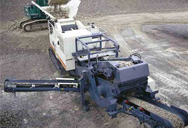
Cement Equipment, Cement Plant Equipment Cement Plant
Cement grinding production. We provide customers with a variety of cement plant equipment and optimize the combination of various types of cement grinding mill to meet the needs of different processes. cement ball mill. Feeding size: ≤25mm. Capacity: 0.65-615t/h. vertical cement mill.
Charlar en Línea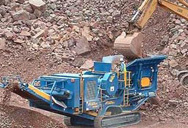
Modernizing cement manufacturing in China leads to substantial ...
2022.11.17 We find that novel suspension preheater rotary kilns account for approximately 99% of cement production in ... advanced techniques and equipment in the clinker ... Machinery Association, 2016). ...
Charlar en Línea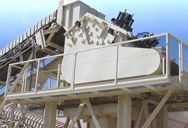
Cement Plant Equipment Technologies for more production!
2019.8.8 The Clinker Plants is up to 50 TPD to 1000 TPD clinker cement plants. 4. Rotary Kiln Plants: Cement Plant’s unit offers high-quality Rotary kiln Cement plants and gives innovation, best quality ...
Charlar en Línea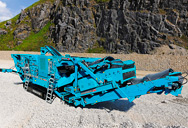
A machine learning approach for clinker quality
2022.7.13 A cement plant of our industry partner is used in this study. As shown in Figure 1, the cement kiln takes the raw kiln feed and thermally transforms this into cement clinker.This process uses multiple
Charlar en Línea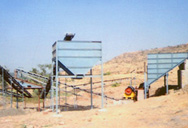
Engineering Design of Mechanical Equipment for
2017.5.1 For fine grinding of cement clinker and additives, ball mills of various sizes are mostly used [1,2,6,7]. These grinding units are distinguished by the simplicity of their design, its operation ...
Charlar en Línea
Cement Manufacturing Process: 6 StepsTo Make Cement Cement Equipment
2020.1.27 6 steps of the cement manufacturing process. When we talked about the manufacturing of cement, anyone who knows the cement manufacturing process slightly will mention “two grinding and one calcination”, they are namely: cement raw material preparation, clinker production, and cement grinding. In the real cement production
Charlar en Línea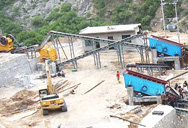
Equipments Used in Cement Process Industry PDF Mill
As a core cement equipment of clinker production, cement kiln is applicable for various materials, such as limestone, clay, dolomite, bauxite, etc. Cement rotary kiln, also called clinker kiln, can be divided into dry-process cement kiln and wet-process cement kiln according to the cement production technology. Dry-process cement rotary kiln is ...
Charlar en Línea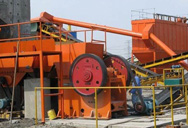
The Environmental Profile of Clinker, Cement, and Concrete: A
2022.1.28 Concrete is the most-used material in the construction industry, and the second most-used after water. Cement is the main component of concrete. A total of 8% of global CO2 emissions correspond to the cement industry; CO2 is the main greenhouse gas contributing to global warming. To mitigate climate change, it is necessary to design
Charlar en Línea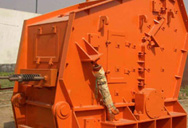
Cement grinding optimisation - ScienceDirect
2004.11.1 The current world consumption of cement is about 1.5 billion tonnes per annum and it is increasing at about 1% per annum. The electrical energy consumed in cement production is approximately 110. kWh/tonne, and around 40% of this energy is consumed for clinker grinding.. There is potential to optimise conventional cement
Charlar en Línea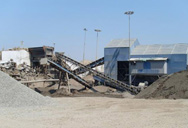
Global Cement Clinker Market 2023 - IndexBox
2023.12.1 The country with the largest volume of cement clinker production was China, comprising approx. 56% of total volume. Moreover, cement clinker production in China exceeded the figures recorded by the second-largest producer, India, sevenfold. Vietnam ranked third in terms of total production with a 3.1% share.
Charlar en Línea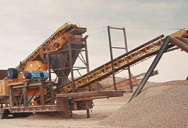
Portland Pozzolana Cement Manufacturing Plant PPC Cement Production ...
Portland pozzolana cement (PPC) is a type of eco-friendly cement which is mainly made of ordinary portland cement clinkers and pozzolanic materials (such as fly ash, calcined clay, etc.). Generally, the constituent of pozzolanic materials in Portland pozzolana cement is 10% ~ 25% by mass percentage. Fly ash is the main ash discharged from the ...
Charlar en Línea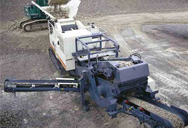
(PDF) Modeling operational cement rotary kiln variables with ...
2022.10.20 Cement production plants are one of the extremest CO2 emissions, and the rotary kiln is a cement plant’s most energy-consuming and energy-wasting unit. Thus, enhancing its operation assessments ...
Charlar en Línea