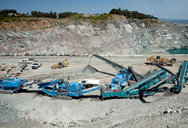
(PDF) GRAVITY SEPARATION IN ORE DRESSING
2017.3.12 Gravity separation is an industrial method of separating two components, either in suspension, or in dry condition, from a
Charlar en Línea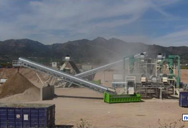
Methods of concentration of Ores – Gravity Separation.
Methods of Concentration of Ores Leaching method. This process is relatively easy but is not considered very efficient. In this method, the ore is... Gravity separation or hydraulic
Charlar en Línea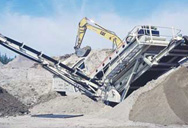
Gravity Separation - SGS
2 AREAS OF APPLICABILITY PRECIOUS METALS (AU AND PGE) Creation of a direct refining vs. to- smelter concentrate Gravity recovery from grinding circuits Separation
Charlar en Línea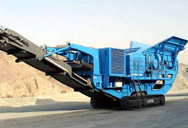
Gravity Separation - ScienceDirect
2016.1.1 Chapter 16 Gravity Separation Show more Add to Mendeley Separation by density difference is a process that is as old as recorded history. Separation of gold
Charlar en Línea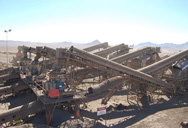
Gravity separation - Wikipedia
Gravity separation is an industrial method of separating two components, either a suspension, or dry granular mixture where separating the components with gravity is sufficiently practical: i.e. the components of the mixture have different specific weight. Every gravitational method uses gravity as the primary force for separation. One type of gravity separator lifts the material by vacuum over an inclined vibrating screen covered deck. This results in the material being suspended in air w
Charlar en Línea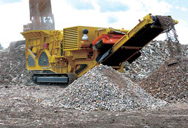
Application of Enhanced Gravity Separators for Fine Particle
separation is replaced by the centrifugal force to usher in enhanced gravity separators. The objective of the present paper is to summarize the applicability aspect of enhanced
Charlar en Línea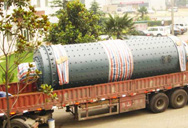
A study of gold ore for processability by gravity separation
2021.2.26 The article deals with the studies of gold-bearing ore benefication by flotation methods. The object of the study is a low-sulfide gold-quartz type of ores with
Charlar en Línea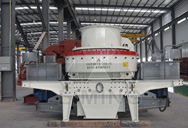
Physiochemical separation of iron ore - ScienceDirect
2022.1.1 For ores with very fine liberation sizes (e.g., below 45 µm), gravity separation is ineffective and a desliming stage is necessary. Zhang et al. (2021) have
Charlar en Línea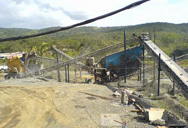
Mineral Processing of Rare Earth Ores SpringerLink
2020.3.26 The principal beneficiation route of different rare earth-bearing minerals includes gravity separation, magnetic separation, electrostatic separation, and froth
Charlar en Línea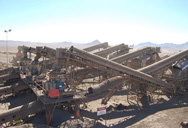
Selection of Gravity Separators for the Beneficiation of the Uljin Tin ...
2016.12.5 Gravity separation is typically used in the beneficiation of tin ores as the density difference between the valuable and associated gangue minerals is significant. In
Charlar en Línea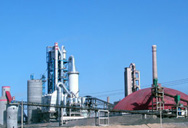
A Beneficiation Study on a Low Grade Iron Ore by Gravity and
2018.8.25 In this paper, a sample from Tange-zagh iron mine was characterized by gravity and magnetic separation methods. The mineralogical studies showed that hematite and goethite are the main iron-bearing minerals with insignificant amounts of FeO. The results indicated that spiral separation yields higher separation efficiency than
Charlar en Línea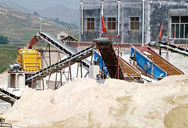
Definition, Methods of Separation, Examples - GeeksforGeeks
2021.11.28 Gravity separation, also known as hydraulic washing, is a separation technique that uses the specific gravity variations between metallic ore and gangue particles to separate the two. Question 3: Give an example of a method for concentrating zinc sulphide ores.
Charlar en Línea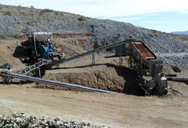
Recent process developments in beneficiation and metallurgy of
2023.3.29 Gravity separation is also used to pre-treat RE-bearing ores. An example of this approach is in use at Maoniuping, where gravity separation by shaking tables is employed after grinding and classifying. The overall grade of the gravity concentrate is 30% REO with a recovery of 74.5%.
Charlar en Línea
Different methods of concentration of ores - Unacademy
As a result, it is categorised as a gravity separation method. The powdered ore is washed using an upward stream of flowing water. The heavier ore particles are left after the lighter gangue particles are washed away. Because tin and lead ores are heavier than gangue, hydraulic washing is used to remove them. Magnetic Separation method
Charlar en Línea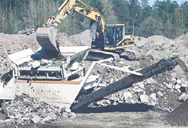
Magnetic Separation SpringerLink
2023.4.13 Weakly magnetic iron ores, such as hematite, need to be treated by a combined process of high-intensity magnetic separation and other separation methods. Some mines of Ansteel Group Corporation used a single method in the early treatment of hematite, such as single-stage flotation or single strong magnetic separation, gravity
Charlar en Línea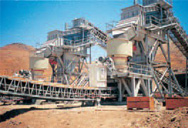
CHAPTER-7 GRAVITY CONCENTRATION OF IRON ORE
The gravity separation processes are comparatively cheap and environmentally friendly. It finds immense application in the processing of iron ores besides coal, beach sands, gold, diamonds, platinum, baryte, fluorspar, tin, tungsten ores etc. The major limitation with the gravity concentration is the treatment of fines and ultrafines. In the
Charlar en Línea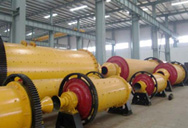
Physical beneficiation of heavy minerals - ScienceDirect
2023.8.1 The efficiency of physical separation techniques of heavy minerals usually encounters some set-backs. The reason is often not far from the inability to develop suitable mineral characterization strategies in order to comprehend/evaluate certain physicochemical features such as surface chemistry, specific gravity difference, magnetic and electrical
Charlar en Línea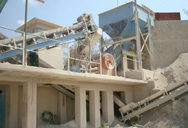
Gravity separation - Wikipedia
Gravity separation is an industrial method of separating two components, either a suspension, ... The rocks are crushed, and while sand, limestone, dolomite, and other types of rock material will float on TBE, ores such as sphalerite, galena and pyrite will sink.
Charlar en Línea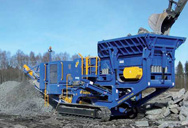
Mineral processing - Wikipedia
Gravity separation is one of the oldest technique in mineral processing but has seen a decline in its use since the introduction of methods like flotation, ... magnetic separation was used to separate the ores. At these mines a device called a Wetherill's Magnetic Separator (invented by John Price Wetherill, 1844–1906)[1] ...
Charlar en Línea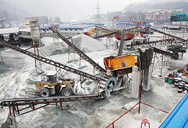
Mineral processing - Concentration, Separation, Flotation
Mineral processing - Concentration, Separation, Flotation: Concentration involves the separation of valuable minerals from the other raw materials received from the grinding mill. In large-scale operations this is accomplished by taking advantage of the different properties of the minerals to be separated. These properties can be colour (optical sorting), density
Charlar en Línea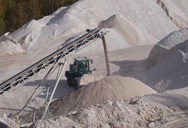
Tungsten ore extraction processing - JXSC Mining
2019.7.4 Wolframite mineral processing method mainly in gravity separation, and includes four parts: pre-selection, gravity separation, concentration and recovery. By pre-selection and discarding the waste
Charlar en Línea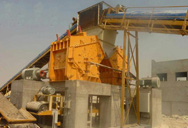
Free Full-Text Gravity Concentration in Artisanal Gold Mining
For ores with fine-sized gold particles and/or high concentration of sulfides, AGM plants combining gravity separation with flotation can obtain gold recoveries above 85%; The adjustment of the length of the stroke and the slope of the shaking tables are critical for efficient separation of fine gold particles; and,
Charlar en Línea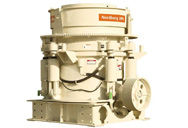
(PDF) Beneficiation of cassiterite from primary tin
2021.11.1 Tin (Sn) content in primary tin ore ranges from 0.2 – 1.0%. The Sn particles liberated in the cassiterite mineral are above 50% so they can be processed by the physical separation method. This ...
Charlar en Línea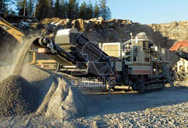
Application of Enhanced Gravity Separators for Fine Particle
2021.3.1 Abstract Beneficiation of low-grade ore is of critical importance in order to meet the growing demand for coal and mineral industries. But, low-grade ores require fine grinding to obtain the desired liberation of valuable minerals. As a result, production of fine particles makes the beneficiation process difficult through conventional gravity
Charlar en Línea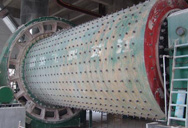
Separation of Fe and Mn from Manganiferous Iron Ores via
2019.8.1 Iron ores can easily be separated from the gangues by exploiting the differences in specific gravity, magnetic, and surface properties [14,15,16]. In addition, it is possible to obtain manganese with a high recovery from manganese ores containing a trace amount of iron via gravity separation methods [17, 18].
Charlar en Línea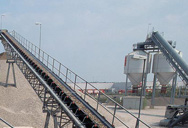
Minerals Free Full-Text Parameter Optimization of the Separation ...
2023.5.5 The current centrifugal concentrators do not continuously concentrate heavy minerals of large mass weight—for example, in the processing of iron oxides. A cyclone centrifugal separator is a new type of beneficiation equipment that has been developed on the basis of the principles of centrifugal separation and hydrocyclones. In this study, a
Charlar en Línea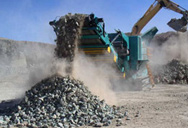
A new method for gravity separation: Vibrating table gravity ...
2019.3.18 A gravity concentrator namely “vibrating table” has been developed with the objective of increasing the product quality of density based physical separation processes. The system is mainly composed of a vibration unit, an inclined chute, TW and WW jets. The principle idea of the separation is to combine the involved forces of a
Charlar en Línea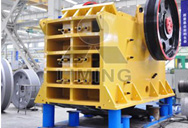
Magnesite Ore Processing: Separation and Calcination
2023.5.12 The processing flow is as follows: 1 Crushing: Use a jaw crusher, roll crusher, and vibrating screen to form a two-stage-closed circuit crushing system to crush the raw magnesite ore to 1mm. 2 Calcination: Send the raw ore into a rotary kiln for calcination at a temperature of 700-800°C for 1 hour. 3 Crushing:
Charlar en Línea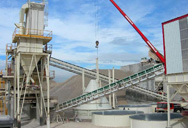
Fluorite Ore Processing Flowsheet and Washing Plant
2021.4.9 Gravity separation is only used for coarse-grained fluorite and is the only method to obtain metallurgical grade fluorite granule or lump. The core equipment of fluorite gravity separation is a mineral jig machine. It can process fluorite ore with a particle size of 0-50mm. Related auxiliary equipments are crushers, vibrating screens, etc.
Charlar en Línea